■ 製造技術
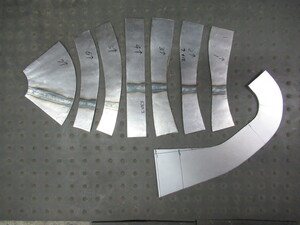
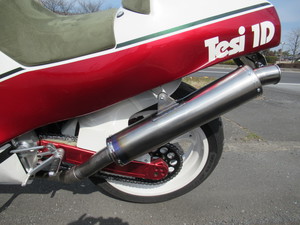
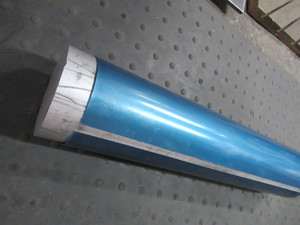
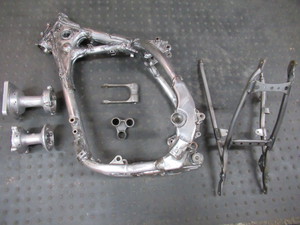
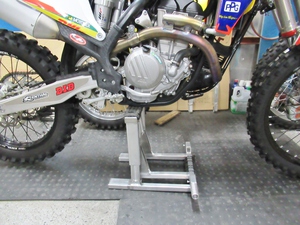
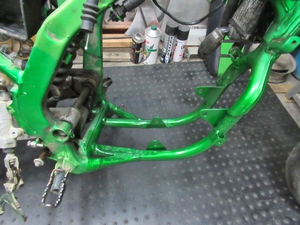
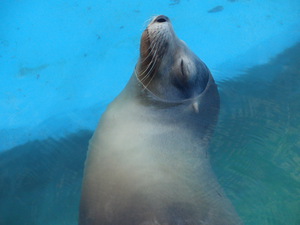
上手く研磨できています。
エキパイ類もこのとおり
よーし、つけるぞー!
その前にノーマルマフラー装着して試乗しなければなりません。
元国際田舎B級の私が、試乗インプレッションいたします。
CB400に動力性能を期待するなんてことはナンセンスです。明らかに旧車デザインのこれはCB360Tの雰囲気を現代風にアレンジしたはずなのです。
国内ロードスポーツのお客離れ、特に我々の世代は若い頃CBに乗っていたりするのはちょっと不良で勉強なんか嫌いな少年たちだった。
岩清水ヒロシみたいなガリ勉が乗っているわけがないのだ。
そして大学で勉強したエリートがデザイナーになって単車作ったって、我々世代の気持ちをつかむデザインや音がするものを作れるわけがないのだ。よって新型ロードスポーツに見向きもしないというわけだ。
(単なる懐古主義なだけなんですがね。スポーツ用のやつはなるべく新しいのにのるべきだと思います。)
根本的にCB360TはツインですがCB400はシングルなので乗り味が違うのは当たり前です。
シングルのデュアルエキゾーストですからエキパイは細くてよいわけですが、見た目ツインマフラーのようにしてあります。
ノーマルは3000rpm以下の低速トルクは弱いですが5、6000rpmのパワー感が良好で一般道で非常に乗りやすい特性でしょう。8000rpm以上回しても加速感は一定でパンチが効いていません。ゆっくりと流す程度に乗るのが一番心地よいでしょう。
そしてツインマフラーに交換して最初に気付くことは「音」です。ノーマルの原付みたいな大人しさに比べて明らかに存在を感じる太い音です。しかも爆音ではないので周りに存在をアピールできる調度よい感じです。走りだして低速から開けていきますが、太いマフラーにありがちな低速の落ち込みは感じません。むしろ抵抗が取れた軽い吹け上がりに変わっています。5000rpmからの加速はノーマルより若干速いかなと感じますが、大きな差はありません。同様に乗りやすいフラットなエンジン特性です。前述しましたがブン回して楽しむ必要のないクルマなので、軽くなったエンジンレスポンスと太い音で快適なドライブができると思います。
なんたってリヤビューから車種が特定できそうもないスタイルを楽しめることが最大の売りです。
排気が抜けるようになるとキャブレターのオーダーも違ってきますが、これは走行中に違和感は特にありませんでした。
通常は抜けすぎると全開時や戻したときにアフターバーンが出ます。吸入空気が多くなってガソリンの割合が薄くなるためです。
これは走行中のアフターバーンは起こりませんが回転を上げてからアクセル全閉で少し出るくらいです。エアースクリューを若干閉めるか、スロージェットをワンランク上げる程度で改善するでしょう。
突然ですが、エキスパンションチャンバーという部品はエンジン部品か車体部品のどちらのカテゴリーに入るでしょうか。
動力性能に密接に関わる同部品ですが正解は車体部品です。エンジンの開発はエンジン設計者が担当し、車体の設計は車体専門の担当者という具合に別々に行われます。また製造もエンジン工場ではエキスパンションチャンバーは作りません。車体関係の部品メーカーが製造します。
では、その手法はエンジンの開発はベンチテストで行われ、排気系の諸元はストレート図で表すまでです。そして車体屋によってストレート図に基づいてパイプを曲げて車体に取り付く形状をデザインすることになります。
今回、手巻き製法のチャンバーを製作しますが、これはプレス成形の型を決めるための前工程となるものです。しかし量産用のプレス型をつくる必要がありませんのでワンオフで終了ということになります。
先日寸法計測したチャンバーのストレート図を基にテーパーパイプを作成して取り回しの検討を行います。
パイプは溶接しないで傾きを調節しながらカーブを決めていきます。
取り付ける車体は極秘なのでお見せできません。
作業の進行状況をお知らせする目的だけです。
フレームやラジエターとの隙間がギリギリに設定されていますので、取り回し検討だけで一日掛かりです。
このパイプは全部開いて展開図となります。
これからが製作本番です。
取り掛かるまで気にしていませんでしたが問題が幾つかあることに気付きました。
それは、見本となる写真と預かった車体の仕様が異なること、チャンバー取り付けに必要なラバーマウント、ボルト類、テンションスプリングなどは一切ついてないこと、サイレンサーの取り付け位置も決まっていないなど懸案が続々です。
なんとかパイプが繋ぎ終わったのですが残念なことにテールパイプの傾きがいまいちです。シートレールに対して前下がりに見えます。
低いラジエターの干渉を避けるためチャンバー位置を下げたことが原因です。テールパイプをあと1センチ上げたいと思います。ここで妥協してしまうことは許し難い結果になります。
こだわりの1センチです。
テンションスプリング付いていますが、見本がここでジョイントになっていたため忠実に再現します。
テールパイプがシートレールと同じ傾きに変更できました。
ホンダ純正のラバーマウントは既に廃番で入手できません。ホーリーさんとこで別メーカーの在庫を見繕っていただき、430用テンションスプリングと一緒に送っていただいたことでスムーズに取り付けステーの加工ができました。
サイレンサーは推定84モデルKA4だと思いますが、リヤフレームとのオフセットを決めるため専用カラーをラバーマウントに装着して固定できました。
実車はお見せできませんが、チャンバーはこのとおり完成いたしました。
実に半年遅れの仕事でした。
明日から1ヶ月ほど身柄拘束されますので電話は出られないと思います。急用には対応できませんが用事のある方はメール送信していただければ、終業後に返信いたします。
量産部品は必ずロット生産されています。ロットの種類や大きさは製造過程における品質特性によって様々です。量産でロット管理しなければならない理由は、材料ロットや熱処理ロットのように納入や処理条件が同一のグループで区別してトレーサビリティー(履歴追跡)を持たせることによって、あとで不具合が発覚したときに選別することにあります。
不具合の追跡調査が出来ないと対象の製品が分からないので改修コストが莫大になることを防ぐ目的があります。
弊社では生産数が少なく一品ずつハンドワークで加工するために部品の不具合は、加工時点で分かってしまいますのでロット生産することはありません。
普通は注文数は1個なので構成パーツは1台分ずつ作りますが、今回は4個一気に作ります。
これだけ作るのに3日も費やしています。
1日1本製作するのが難しいアルミサイレンサーです。
構成パーツを溶接組み立てしたところです。
部品が揃っていれば連続溶接できるのですが、同じ姿勢を長時間続けることによって血行不良になります。
エコノミークラス症候群という症状ですが、私の場合は肩こりや腰痛になってしまいます。
もう年寄りですね。
溶接完了したらバフ研磨です。夏場と違って体が温まるくらいなので助かります。
研磨は自社製品しかやりません。
お客さんに頼まれても専門の業者さんを紹介するだけです。
ここまで出来れば、グラスウールを詰め込んで組み立てるだけです。
明日の段取りを考えながら発送の準備します。
おまけはCBヨンフォア専門店シオハウスさんからお借りしたVMXマガジンから
ジム・ワイナートとトニー・ディスティファーノの接戦です。
トニーの顎にジムの左グリップが入っていますね。
トニーの右ブーツはジムのフロントフォークに引っかかっています。
ものすごい勝負への執念です。安全運転至上主義の私は見習いたいです。
ここに無限ヘッド(CR125R)があります。ヘッドガスケットが廃番になっていて、代替のガスケットを作る必要がでてきました。
ホーリーさんとこでシリンダーに傷がついた無限をスリーブキットで再生したのですが銅板ガスケットが圧縮漏れでよくないと聞いて
お節介に「水冷ヘッドにはバネ鋼のガスケットが良いでしょう」と提案してしまった責任を取るためにメタルガスケットを作る役を請け負うことになりました。
昔、ボアアップで純正のメタルガスケットのボアを拡大したことはありましたが、材料から新造した経験はありません。
これは自己啓発として就業後に少しずつ進めますので作業日誌は後日アップいたします。
87年型CR125の純正ガスケットも見本としてお借りしていますが、材質はアスベストです。アスベストは耐熱性が高く、弾力もあるので高温での気密性に富んでいると思われます。
ヘッドガスケットに必要な性能は高温でもバネのような弾性をもっていることです。
シリンダーヘッドはM8のスタッドボルトで締め付けられますが、この締め付け荷重はどれくらいのものかといいますと
エンジン関係に使用されるボルトは100kg級の強力ボルトです。材質はSCM400(旧435)で、めっき可能な最高強度のボルトになります。めっき後のベーキング(水素脆性除去処理)が必須です。
足回りに使われるボルトは120kg級ですが、高負荷で亀裂を防止するため、めっき処理は不可で通常は耐食性にすぐれたダクロコートを施します。
100kg級の意味はmm2あたりの引張り強度が100kgということで、強度区分で10Tと表記されます。80kg級は8T、以下7T、6Tという具合に材質と熱処理の違いで強度を設定しています。
ではヘッドのスタッドボルトはM8ですから有効断面積(ねじの呼び径ではなく、ねじ底の断面積)は36.6mm2で引張り強度3400kgですがこれは垂直に引っ張ったときの破断荷重なので、ねじの締め付けでは耐力2894kgで考えます。
耐力というのはボルトを締め付けたときの軸力と伸び(またはトルク)線図で直線で表す領域(弾性域)から0.2%軸力が下がった点(降伏点)を耐力と定めています。
実際の締め付けでは降伏点を越えるとボルトが永久伸びを起こしてしまいますので、降伏点直前がボルトの限界になります。ボルトの規定トルクは、降伏点に達しない上限と緩みが発生しない下限値が指定されています。何故規定トルクに幅があるかというと、締め付け座面やネジの状態でμ(摩擦係数)が違うために軸力がばらつくためです。締め付け作業はトルクレンチを用いたとしても締め方によって軸力が変わります。レンチを締めるスピードや回数で、同じ目盛りでも軸力が変動します。
ネジ山や座面が滑っている状態を動摩擦、止まった状態から再度締めるときは静摩擦と呼び、静摩擦の方がボルトを回転させるのに大きなトルクが必要になります。締めすぎたボルトを緩めるときに大きなトルクが必要なのは、このためです。
話を元に戻します。スタッドボルト1本あたり2800kgの締め付け力とすると6本で16.8トンの荷重がヘッド面に掛かっていることになります。この荷重に耐えられる硬さのガスケットが必要と考え、バネ材を仕入れましたが、純正部品の材料は一般の鋼材屋で扱ってないことから、それに近い性質のステンレスを選定しました。
これからガスケットの加工に入りますが、これくらいの形状ですと図面を書いてレーザー加工を頼んだ方が安上がりで加工精度もよいと思いますが、ここでは手持ちの加工機でどこまで出来るか試してみたいと思います。
使用する道具は板金ハサミ、ボール盤、旋盤くらいです。
最初はスタッド穴基準とするため穴位置を割り出してマスター板を作って下穴を空けていきます。
ステンレス板にスタッド穴を空けておきます。
スタッド穴基準でセンターと外周を旋盤加工するための加工治具はこのとおりです。
ステンレス板の外形は板金ハサミで荒く切っておきます。これら6枚を重ねてフランジにボルト締めして加工を行います。
フランジで挟むことによって薄板の剛性があがってバリの少ない切削面に仕上がります。
旋盤で外径φ101、内径φ55に加工しました。
思ったとおりバネ材は硬いです。
超硬チップで切削しますが刃物の消耗が早いです。
下穴はハイス(高速度鋼)のドリルを使うので、重ねて穴空け加工は困難です。
ウォーターラインを同等にするための見本です。
排気側の長穴を空けるのにフライス加工だと材料が硬いのでエンドミルが割れて全部ダメになることを恐れ、地道にドリルで下穴を開けました。
穴が繋がったところで、切り残した部分はヤスリで手仕上げすることにします。
アルミホイールやメッキシリンダーなどバリが出る製品は量産でも手仕上げでバリ取りするものですから、手仕上げは立派な加工工程なのです。敢えてハイテクを使わないでハンドワークで処理することが我社の物作りの原則です。
加工治具は使い捨てになります。
量産のメタルガスケットはウェーブ加工されており、穴の周囲を囲むように凸の部分が当たって密着するようになっているのでバネ材が必要なのでした。
しかし、これは平面で密着させる構造なので、シリンダーヘッドの平坦度とヘッドナットの締め付け力が成功のKEYであると考えられます。
1年ほど放置しておりましたCRM250の2WDの続きです。
この車両は2輪駆動車の走行性能を確認するための実験車両なので、MXやEDを目的としているのではありません。前輪を駆動する方法やその運動性能について、机上の理論や想像で語る人は時々見かけますが、実際に走行可能な車両を作った例は非常に珍しいので、廃却されるのが惜しいと思って動く状態で保存しようと思ったのです。
実は某2輪メーカーで、これと同様の機構で試作車両を作り実走テストまで行いましたが、安全性とコスト高、舗装路面における不具合などの理由で市販車としては不適切と結論つけたものです。
おかげで世界に1台の稀有なマシンになりましたが、動態保存するためには時々走行確認する必要があります。
前回フロントタイヤが老朽化のため18インチのフロントタイヤを交換しましたが、サイズが太すぎてハンドリングが重かったので、今回は幅の狭いトレールタイヤに交換しました。
DL、D603 3.00-18
前回フロントに履かせたK695はリヤにコンバートしました。
100/100-18
2WDの場合前後のタイヤ周長が同じでないとタイヤの周速に差が生じて、タイヤや駆動系に負荷が掛かってしまいます。
直進時は問題なくとも、コーナリング時にトレッドの横に接地面が移動するため、周速が前後で違ってきます。それが舗装路でのハンドリングの重さに繋がったり、フロントに駆動力があるために、アクセルを開けたときにオーバーステア気味になるなど、通常の後輪駆動車と比べるとクセがある乗り味となります。
この方式の真価はフロントが回らなくなるような泥、砂地や急勾配で発揮するものです。
普通路面では後輪駆動車に対してメリットはありませんが、癖のあるハンドリングを味わってみたいと思います。新しい乗り方を追求してみるのも良いかもしれません。
一年以上ぶりに乗りました。コースはジャパンVETの前日で綺麗に整地された路面でしたが、フロントのストロークと減衰不足でコーナー新入のギャップで底突きます。ジャンプを飛んだ場合はもっと恐ろしいショックを受けるため、ジャンプ区間はスローダウンするしかありません。
コーナリング特性はやはり独特で乗り慣れるのに20分2ヒートが必要でした。
散水後のスリッピーな路面は当然前後タイヤが滑るのとフロントヘビーなので慎重になりますが、フロントタイヤに駆動力がありますので前輪が引っ張っている感覚が味わえます。
三つ又の幅はハンドルを切ってもチェーンが当たらないギリギリの寸法ですがフロント18インチのためかギャップで激しく振られることがあります。スピードを出したギャップ走行は要注意です。
結局通常のMXマシンよりギャップの浅いところを狙うとか、フロントから突っ込まないように工夫して走りますので体力が必要で、よいトレーニングになりました。今度MXマシンに乗るときが楽しみになりました。
周りのパドックに現行車は見当たりません。非常に楽しい雰囲気です。
83年型CR250は私が関東選デビューしたマシンと同型です。
新入社員で田舎者でしたから、プレイライダー誌(森岡さんが作った雑誌)の広告をみて、最初はモトレオン(後のロッキースポーツ)へMXer買いに行ったのですが在庫がなくて、帰り道にあったモトバムに寄ったら「取り寄せてあげる」といわれて初めて新車を買うことができました。勿論ローンでしたけど
こんなマシンもあって感激です。81年型無限ファクトリーマシンですがラジエターはアメリカのビルダーさんによる新品だそうです。
スイングアームはコークボトル、インテークとエキパイにはサブチャンバーが取り付いていたり、市販車と違う部分が多くてワクワクします。
81年型CR125は学生時代最後に乗ったマシンと同型で懐かしいです。
綺麗なKX250、75年型。私は中学1年生でした。このころは未だMXに出会ってなかったですが、月刊MC誌のカタログで知っていました。実車に2013年に出会えた奇跡です。
しかもオーナーの田山さんがビンテージクラスで快調に走らせているのを見て、飾りじゃないことを知りました。
他にもたくさん懐かしいマシンがありましたが、カスタムマシンではこれが目をひきました、上山さんのXT500.ビッグシングルなのに走りもよくて、エンジン、サスなどかなりチューンアップされた話を伺いました。
これをみて、鈴木忠男さんがXT500改で全日本参戦していたのを思いだしました。
体力トレーニングも出来たし、珍しいマシンも見れたし、結構満足できた一日でした。
今週はドリーム50のアルミタンク製作です。お預かりして5ヶ月くらい経過していますので、お客さんも待ちくたびれているかもしれません。
依頼内容はRC116のような形のタンクにしたい、ということです。
実車はホンダコレクションホールにあるのですが、2月末まで館内改装のため休館です。
仕方なく画像を見ながら作ってみることにします。
しかし、驚くほど細長いタンクです。
作り始めてみますと、RC116とドリーム50はフレームのレイアウトが全然違うことに気がつきました。
おそらく、ドリーム50はサーキット走行だけでなくツーリングに使っても支障ないようにシート幅が広くなっています。そのためシートレールも幅広ですから、こちらのフレームに合わせたタンク形状にしないと取りつけが困難なことがわかりました。
画像は底板の上にタンク上部と横板を仮止めして形状確認を行っています。
板金で成形したアルミ板を溶接で繋ぎます。
外側の溶接ビードは研磨して消しますので内側の溶接をしっかりとつけておきます。
明日外側の溶接作業にかかります。
かなり進行しているように見えますが、完成まであと3日くらいかかるでしょう。
普通のタンクはメインパイプの上まで被さっていますが、このタンクはシートレールの上まで伸びていますので、トンネルの形状が複雑になります。
2枚の隔壁はガソリンの移動を抑える目的とタンクの剛性を上げる目的があります。
RC116はワークスマシンですが、ドリーム50は市販レーサーCR110に似せて製造されたマシンですからフレームの構成が違うわけです。
ガソリン溜まりにコックを取り付けますが
本体への溶接は研磨後にします。
突起物が無い状態の方が取り扱いしやすいためです。
RS125から移植するタンクキャップも同様です。
溶接はひととおり終わり、接合部の研磨と表面の均しを大雑把に行いました。
タンク容量は7.0Lです。ノーマルの容量は知りませんが、DE耐とか走るようでしたら気になるところですね。
ノーマルはCDIユニットがシートレールの上にはみ出しているため取り付け位置を変更してタンク底板をフラットにしてあります。
前下がりだったノーマルタンクはガソリンが前方に残ってしまい最後まで使いきらないらしいですが、このタンクは水平になっていますのでガソリンを使いきれるでしょう。(給油量を制限される耐久レースでは有効です)
ニーグリップ部分はシートレールより狭くなっています。RC116はもっと狭いですが、フレームとのマッチングでこれくらいが狭さ限度でしょう。
本来は赤色塗装ですが、お客さんの要望でアルミ地肌で終了です。
お客さん独自のプロジェクトがある限り私の業務も続いていくでしょう。
仕上げにサンドペーパーで磨きました。ハンマー痕や溶接ビードなどで表面の細かな歪みを平滑に均していきます。
60番から磨きはじめて180番で止めておきました。鏡面に仕上げるよりこれくらいの粗さの方が塗装の密着はいいでしょう。さらに磨きこんでポリッシュすることも可能ですが、あとはオーナーに委ねます。
ホンダはHSV010でGT500に挑戦しているというのに、このプロジェクトは何とささやかなものか。
全部手仕上げですからね、ハイテク一切無し!
カーレースの方はホンダのお家芸だと思うのですが、GT500では苦戦を強いられているようです。
技術力だけでは負けないと思うのですがそれだけじゃないんですね。
F1よりこっちの方が道路で乗れるクルマに近いので好きですね。絶対乗れないわけですけど、少年時代のスーパーカーブームを彷彿させます。
もてぎ貸切で極秘テストですかー
金持ちのレーシングチームは違いますね。というより、サーキットも自社所有でした。
研究所もテストコースも部品メーカーもなんでも揃っているのに何故、勝てないのか!
今年こそはレーシングスピリッツ見せてもらいましょう。
しかし、この顔 強そうやな。
エキパイの鍍金が仕上がりましたので、マフラー製作の続きです。
今日はマフラーのジョイント部分とマウントステー作りに取り掛かります。
見本は量産品ですから、全て金型を用いてプレス成型により作られたものです。
量産は少なくとも千個ロットの生産だったでしょう。マウントブラケットなどは下請けのプレス工場などに外注して大量生産して安価に作られたものです。
しかし、当方には金型などありません。見本の形状を真似て成形するしかありません。充分な予算をいただいてあれば安心して立派なものを作れるのですが大概の部品は製作に費やした時間分の全てを請求するわけにはまいりません。それは、必要な生産設備が無い上に初めて成形する部品であるために、長時間を要するためです。
これはジョイント部分ですが、非常に凝った形状であります。
ボルトを差し込む部分が袋状になっており、左右で4個のフクロを作って溶接で取り付けしてありますが、この部分だけで半日費やしています。
これができれば、エキパイにマフラーを差し込んで、位置決めに掛かれます。
メガホンの溶接ビードは全て消してあります。
溶接のまま研磨屋に出しますと、ピンホールやハンマー痕などが残ってしまって、鍍金の仕上がりに影響してしまうため、研磨の下地はこちらで整えておかなければなりません。
研磨は全てお任せでは、上手く仕上がってこないことが分りました。
ちょっとユニークな形状のマウントブラケットです。
上は見本ですが、なるべくノーマルのデザインを崩さないように真似ています。
締め付け面の凹ましが必要なので、イレギュラーな方法で鉄板を成形してみました。
鉄板はなかなか、言うことを聞いてくれません。
なんとかマウントブラケットの成形ができたので、左右マフラーの取り付け位置を確認しながら溶接しました。
あとはエンジン下側に付けるマウントステーが残っていますが、今日はここまで。
明日、最後のステー取り付けを行って研磨屋に持っていく段取りが整うはずです。
日付が変わって、エンジン下部に取りつけるマウントステーを作って溶接しました。
2枚合わせのステーですが、これも純正になるべく似せて作ってあります。
純正に似せる理由は、それ単品で見るとオリジナルだと思わせるようにしなければならないからです。
復刻されない希少なパーツを新品で再現するということは、旧車の維持には不可欠なことで、商業的に利益を得る目的の「偽物ブランド」とは全く次元の違う話だと思います。
オリジナルと再現品を並べてみます。
B級マフラーと思いますが、大体同じ形状に出来ているでしょう。
鍍金が仕上がってきて、ピカピカになれば、素人さんならどちらが本物か見分けがつかないと思います。
これで私の作業は終わり、研磨屋に持っていってカネを払ってくるだけです。
ここまでエキパイと合わせて10日ほど掛かりましたが、一段落ということで会社なんかだと祝杯を上げたりするでしょうが、私にはあのような発酵した水など飲んだら気持ち悪くなってしまうので祝杯は上げません。そのかわり、気持ちよくなる音楽でも聴くとしましょう。
スパイロ・ジャイラのモーニングダンス。ものすごく爽やかな気分になります。寒気が来ていますので気分だけでもトロピカルでいきましょう!サンキュー、Mrベッケンスタイン(SAX)
'>1979年リリースの楽曲ですから、34年も経つのですね。カセットテープが擦り切れるほど聴いていましたが、何年経ってもエエモンはエエ!
バックオーダーは1ヶ月分残っていますので、社外品マフラーの修理は優先的にはできません。2ヶ月以上お待ちいただいているお客さんの注文がありますので順番に進めております。
不運にもマフラー壊してしまった場合は、新しいものに交換されることをお勧めします。
また実車は殆どありませんので取り付け確認などが必要なほど変形している場合も保証できないことをご了承いただきたいと思います。
カーボン樹脂製のエンドキャップが割れてしまって交換が必要ですが
補修パーツもありませんので、鉄板で作って代用します。
ビレットパーツのマウントステーですがリベットが外から外せない構造でしたので、ボディーを切って内側のフランジを削除して外しました。
マウントステーの面積が小さいので加重を受けるとボディーに食い込んでしまう難点があるようです。
チタン材は非常に高額になりますので、アルミ板でボディーを作って代用します。
修理というより半分製作という形になります。
メーカーから補修パーツが販売されることが理想だと思います。
マウントステーの取り付け位置は全く不明なので実車をお借りしてマーキングしてから取り付けることにしました。
今回は隣の川越市在住の国際A級ライダー松本耕太選手のガレージにお邪魔してきました。
彼はお父さんの会社で働いているのでお給料でチャド・リードと同仕様の前後サスペンションを購入してCRF450Rに奢っています。モトクロスは気が向いたときだけ乗るというお気楽モードが信条のようです。レース出てもお金になりませんからね。
NSR250R 89モデルです。これはチャンバー製作のためお客さんに持ち込んでいただいたものですが、私が会社員時代に新車で購入して乗っていました。
2年ほど通勤やツーリングで使用しましたが出張が多くなり、オートバイとも不縁になりがちで段々乗らなくなり手放してしまいました。
あれから25年も経つのに、このように綺麗に保存されている人がいることに感心します。
買いなおそうと思っても、この年式は高額になっていることと、純正部品も絶販が多くなってきていますので止めておきます。チャンバー製作記は後日(1ヶ月ほど)掲載することにして
今回の題材はこれです。
純正のサイレンサーですが、この何気ない部品に非常に高度な鍛造技術が使われています。
このボルト締めのフランジ部分と筒が一体成型であること、この製法が想像できるでしょうか。私は別の部品製造の打ち合わせで某鍛造メーカーへ出張したときに、この部品を見つけました。ホンダが発注するサイレンサーのメーカーは別にあるのですが、その会社から手配された2次メーカーだということです。
一般的には認知される企業ではありませんが鍛造専門として自動車工業界を支えている重要なスポットにあると思います。当時の打ち合わせの目的は、設計からは図面が出され、購買部でメーカーを選定して発注する、製作所では部品を受け入れて組み立てる。という自動車製造の流れの中で部品メーカーと受け入れ側の取り決めを行っていないと、担当が別々の人間が行っているので勝手に作られると量産が成り立たなくなるためです。
搬入の何週間前に発注するとか、ロットの大きさ(一回に製造する数)などは購買で取り決めします。私の担当は受け入れる部品に不良が混入しないための取り決めです。不良の検出は検査によって行いますが、製造工程で不具合を出さないことが重要で、そのための重点管理項目はどのようになっているか、現場ではどのように行っているか、実際に確認する必要があります。
そんな製造現場で見てきたものの中にこのサイレンサーのような一体成型があったわけですが、特殊な金型と大型のプレス機を使って、ビレット(仕込み重量と形状を管理された材料)を金型に押し込み、筒の部分は金型の隙間を滑りながら伸びてくるという、想像を絶する塑性変形を伴います。
通常は冷間で行うようですが、このような変形抵抗の大きいワーク(製作物)は必要におうじて加熱炉で温めて柔らかくしてから鍛造します。ここで、非常に高荷重で金型と材料が滑って変形していきますので金型と材料には特殊な潤滑材も塗布されています。
普通の鍛造はワークの型抜けを考えて「抜け勾配」がついているものですが、これは抜け勾配ゼロなのです。押し出し成型に近い製法であることが伺えます。
これがエンドキャップ部分ですがフランジを内側カーリングで荷締めて固定されています。
これで非分解部品となるわけですが、ここまでの工程でサイレンサー外筒部分にフランジのタッピング以外に加工はありません。
全て金型と専用機で成型しますので人間の手作業はワークの運搬だけということになります。
品質は工程で作られるもの、人為的なミスや熟練の度合いで製品がバラつくことを防ぐということが量産の考え方でした。
なにしろ切削加工なしでサイレンサーが出来てしまいますので、無駄がありません。こういうことを業界用語で「歩留まりがよい」といいます。厳密にコストが算出され、安価に提供せよという親会社からの要求に応えた形ではないかと思います。
今の私の仕事は全く逆のことをやっています。量産はできないので、一個だけ作る人為的技術が製品の可否を左右します。おそらく量産を経験していないと、こういう発想も起こらなかったでしょう。
チタンパイプに砂を詰めて手曲げします。
これはφ35ですが180°曲げは相当な経験が必要でしょう。
バーナーで炙りながら金属の固さを腕に感じながら柔らかくなったところで曲げていきますが、失敗するとパイプが潰れてしまったり、内Rにシワがよったりします。
曲げ可能な最小Rというものがありますが、これは内Rで45Rです。太いサイズほど曲げRは大きくなっていきます。
ベンダーマシンはありませんので、手曲げ技術だけが頼りの作業です。
YZ250Fのノーマルエキパイを切ったものと比較ですが、遜色ないカーブを描いています。
オフロード用のエキパイはこれができないと形になりませんので必須テクニックでしょう。
フランジの部分ですが、YZは口元が2mm拡大しています。フランジで押さえるためのツバ出し加工もしてあります。
フランジはA2017削り出しです。量産ではチタンやスチールのプレートをプレス打ち抜きやレーザーカットするのが普通ですが、スタッドボルトの締め付けで撓んでしまいますので、A2017の厚さ10mmのほうが、撓まず放熱性も良いので採用しています。
後半のパイプはφ41.3ですが材料代が2mで16000円と高価なもので、2万円のエキパイを1本だけ製作すると完全に赤字です。2本作って材料代が払える程度ですから厳しい商売です。
こんな感じで購入した材料代を回収するために日々、仕事に励んでおります。
何故これを作るかといいますと、ノーマルエキパイに亀裂が入ったり、潰れたりして、修理を頼まれることがあります。修理可能な程度には限りがあります。その場合は新品購入をお勧めするのですが純正品でも相当高価なもので、なるべく出費を抑えたい要望に応えようとしているわけです。
再生中だったCRM250の2WDですが、欠品していたフロントフォークのスプリングが組み込めましたので、走行可能な状態になりました。
世の中の多くの理論は聞いた話や本で読んだりした知識に基づいています。実際に体験したことと見たり、聞いただけの知識では、理解の度合いに大きな隔たりがあるものです。やってみなければ、答えがわからないから無駄なことに、お金をいただくわけでもなく大きな労力を費やしてきたのです。そして4輪メーカーがあれだけ多くの4WD車を普及させてきたのに、2輪の2WDが普及しない理由を身をもって体験したのでした。
この車両がトレール車のスタイルをしているため、試乗にはMXコースが適しているだろうと思いオフビレで走ってみました。
平な路面は、当たり前ですが普通に走ります。前後輪が互いに駆動力を持って転がっていくので両輪が別々の方向へ向かおうとします。そのことが独特の直進性とハンドルの重さを発揮するようです。この時点では普通の1WDの方が乗りやすいでしょう。
このクルマの構造上、MXコースを走るには問題がある点が大きく二つあるように思われます。
一つはこの三つ又の幅、ハンドルを切ってもフロントのチェーンが当たらないギリギリの幅ですが、ノーマルのそれとは大きくことなります。同時に幅広のフロントタイヤ、フロントアクスル。これらがハンドルを切ったときの慣性モーメントを増大させ悪影響を発生します。特に高速でギャップを通過するときに路面からのキックバックを激しく受けてハンドルを揺さぶります。抑えるのに相当な力を要しますので、危険でしょう。
二つ目はフロントの重量、駆動系とフロントホイールなど、おそらく10kg近く増量に加え、フロントフォークが89年式のノーマルなので、明らかにサスペンション性能不足です。中型のオンロードバイクでジャンプを飛ぶくらいのイメージです。あっさり底突きしてしまいますので、深いフープスや連続ジャンプの走破は無理でした。そもそもMXではフロントを上げてギャップを通過するテクニックが必要ですが、このクルマでは苦手です。こういう結果でオフロードをハイスピードで走ることには適さないという結論に至りました。この2WDの真価を発揮するには、グリップの悪い登坂路面か、タイヤが潜ってしまう泥か積雪の路面のような場所が適しているでしょう。また機会があれば、雪が積もった日にこのクルマを持ち出して試乗してみたいと思います。1WDでは走行不能なコンディションであれば2WDのすばらしさを堪能できると思います。
以上が2WDが市販されない理由だと思いますが、この問題点をクリアさせる技術開発をおこなったとしても販売台数的に利益が見込めないと2輪メーカーが判断したと想像します。いずれにしても、貴重な実験車両を保存して、いつでも走れる状態にしておきたいと思います。
英国のバーフィールド社が発明したのでバーフィールド型等速ジョイントと呼ぶこともあります。国内では富士重工と東洋ベアリングが共同開発して1966年にスバル1000に装備されたのが始まりとされています。
オートバイの2WDにはこのメカニズムが必要不可欠といえるでしょう。
正立フォークの2本のアウターチューブを繋ぐ形で取り付けられる等速ジョイント。ジョイントの揺動中心部をステアリング中央に設置することにより、ハンドルを切りながらチェーンでフロントホイールに動力を伝達することが可能になります。
2軸の回転運動を伝える継ぎ手としてユニバーサルジョイントがありますが、これでは軸の交差角度によって回転速度に変動が生じます。また7度以上の切れ角で振動が著しくなって円滑な運転ができなくなります。これは回転数と同じ周波数でフックが揺動を繰り返すことが振動の原因になるからです。
等速ジョイントではこの問題が解決されていて、2軸の回転数を等速で、交差角度がついても円滑に伝えられることができます。
4輪車ではFFや4WDには必ず装備されているメカニズムでもあります。これは、駆動輪が操舵輪を兼ねているためで、サスペンションの揺動とステアリングの操舵と同時に軸が回転運動をするという複雑な動きをしなければ成り立ちません。
別名ダブルオフセットジョイントともいいますが、ディファレンシャル側を入力軸(インプット)、ホイール側を出力軸(アウトプット)と表現します。どちらも軸の先端にボールベアリングを装備して相手側の軸にボールを受ける溝を掘ったケースが一体となって動力を伝達します。
インプット側は変動する軸距離を吸収するようにボールがスライドしながら回転運動を伝達します。
アウトプット側は両軸間角度の2等分面上にボール溝を配置したケースがついて、操舵による揺動と回転を同時に伝達して、ハブ&ディスクに繋がっています。
これら等速ジョイントの製造にはベアリング用の鋼材を冷間鍛造と砥石研磨、熱処理という工程を踏んで作られています。本田車の等速ジョイントは栃木県の真岡製作所で内作されています。ボールベアリング部分はNTN東洋ベアリングから支給され、ボール溝のついたケースを製造してアッセンブリーしています。
冷間鍛造で溝の形状を成型し、ミクロン代の精度で砥石研磨で仕上げられます。その後、高周波焼入れで所定の硬さに熱処理されますが、加熱方式は連続炉です。治具に固定されたワーク(加工物)をベルトコンベアでトンネル型の連続炉に通し炉中の温度と加熱時間を管理されます。浸炭焼入れなので炉中雰囲気は炭酸ガスで置換されます。
高周波焼入れは部分焼入れとも呼ばれ、製品の形状毎に製作されたコイルで誘導加熱されます。加熱が充分に達すると水スプレーで急冷されて焼き入れ完了します。材料の粘り強さを持たせるため、連続で焼き戻しされます。
処理後の重要な品質特性の一つ表面硬さですが、これは熱処理ロット毎に抜き取りで破壊検査となります。ロックウェル硬さとマイクロビッカース硬さですが製品を平面にスライスして鏡面仕上げした面を測定するため検査品は破壊となります。ロックウェルCスケールでHRc58以上、マイクロビッカースで硬化層深さまで測定して品質保証されます。
この2WDに使用された等速ジョイントは車種は不明ですが、軽自動車のものと思われます。ゴムブーツが破れてグリスが飛散したためブーツ交換を行いました。塗装の剥離した部分を再塗装して組みつけたいと思います。
NSR50のロードレーサーが今回の議題。
GPmonoでレースをされているナオキさんの練習車ですが、ミニバイクは転倒も多いそうでダウンチャンバーだと、サイレンサーは路面に擦ってしまうため
サイレンサーをリヤカウルの中を通す、センター出しに改造するためチャンバーをアップタイプに変更してフレームの中を通すレイアウトに作り変えるというもの。
チャンバーを作るとき、最初にやることは元になるチャンバーの寸法を測ってストレート図に書き直すことです。
写真の上側は元のチャンバー
下側はストレート図に基づいて作られた模型
円盤はパイプの内径を表し、軸芯の棒はパイプの長さを表します。
この模型を曲げて車体に取り回すレイアウトを検討します。
このようにエンジンやフレームとの隙間を確認しながら形状を決めていきます。
同じものは二度と作りません。この車両だけのためのワンオフ製作です。
このあとアンダーカウルやキャブレターの燃料ホースなどに当たらないようにクネクネと複雑なカーブを描いて、狭いフレームの隙間にチャンバーが収まっていきます。
明日は模型の形状に合わせてパイプを成型していきます。
成型されたパイプを接合しました。
模型のカーブに似ていますが、車体がアップチャンバーを想定して設計されていないために取り回しはミリ単位でフレームをかわすシビアなものになりました。
アンダーカウル装着のため、フレームギリギリに寄せないと、グラスファイバーのカウルを溶かしてしまうことになります。
明日はラジエターのマウントとセンター出しサイレンサーのフィッティングを行います。
震災の前日から製作に取り掛かっていたタンク作りですが、3日ほど動揺して通常の業務ができませんでした。とりあえず、やりかけた仕事を完了させるべく再開しましたが、計画停電で一日のうち3時間くらいは業務中断になってしまい、非常に効率悪いです。
被災地の電力不足、燃料供給不足を考え、工場の空調や石油ストーブを止めてやっております。幸い寒冷地ではないので、寒いですが我慢しながら仕事しています。これも支援の一つと考えております。
義援金や救援物資だけが災害支援ではありません。最も強力な支援は国の力だと思うのです。自衛隊や消防庁に指令を出したり、車両を動かしたり、職員の人件費を払ったり、全て税金でまかなうのですから被災していない地域の人ができる最も重要なことは、今やっている事業をしっかりと遂行して税金を払うということであると思っています。
アルミ板金でこしらえたガソリンタンク。
オーナーさんはジムカーナでNSR250に乗っていますが、ノーマルタンクの張り出しが大きいことと、エアクリーナー吸気口を塞いだデザインを改善するという目的でタンク製作に踏み切りました。
フィラーキャップはノーマルを使用していますので鍵を使って開閉します。
タンク底板の形状です。エアクリーナーボックスを逃がすデザインです。
中央付近に二つ穴が設けていますが、フィラーキャップの構造上、エアベントと水抜きのパイプがタンク内部を貫通しています。
車体に装着した様子です。
フューエルコックは左下に設置してあります。
レーサー用の部品で、リザーブ無しです。
タンク容量は13L、大体これでご要望にお答えできると思います。
停電や燃料の調達が悪く通常より効率悪いですが、まだまだバックオーダー抱えておりますので、なるべく早く仕事を進めていくだけです。
連日猛暑日であろうと、世間はお盆休みであろうと、私には関係ない。
大勢のお客さんが私の作るマフラーを待っていることも充分承知しているが
どうしてもやらねばならないことがある。
これをつけて走るとどの様な喜びがあるのかは私は知らない。
これは私が考えて作ったものではないが、作った人に再び頼めない理由は
製作者がやめてしまったためであり、既に廃盤の商品になっているからだ。
それなのに、この見本だけで製作に必要な加工寸法を割り出し、材料を選定し、切削工具も購入し
取り掛かっている。
おそらく全工程に費やす時間は100時間を越えるだろう。
時間工賃を1000円で計算しても10万円になるが材料代や工具代は別に実費で払わなければならない。
おそらくこれを希望するお客さんは、そのような計算は一切、頭の中にはないだろう。
もちろん、掛かった全額をお客さんに請求するつもりは毛頭ない。
最初から利益にならない仕事だということを私は分っていたからだ。
それでは何故、儲からない仕事を引き受けたかというと
やってもいないことを、大変だということが嫌いだからだ。
自分がやって経験したことだけが、語っていいことだと思っているからだ。
アルミの塊からマニュアルのフライス盤で削り出す。この加工時間を加工しないで算出できる人がどれだけいるだろうか。これはピボット部分のパーツ
土曜日夕方までかかってここまで出来た。
クッションブラケットとリヤアクスルのパーツ。図面が無いので寸法計測しながら加工していくので
非常に時間がかかる。明日のレースの整備があるので、これにて中断。
本日はアーム製作。
手前がアームの型で、上の4つが絞って出来たアームの部材。
作り方は教えてもよいが、割愛しておく。
よく、作り方を自分で考えないで他人に聞く人がいるが、
調べたり、トライする努力なしに安易に情報を得ようとする行為なので適当に答える。
自分で考えて物事を運ばない人は、新しい物を考案する能力は得られないと考えられるのだ。
アームを溶接で接合してから、スイングアームの形状に合わせて曲げてある。
組み立て治具に各パーツを固定し、仮留めする。いよいよ本溶接ができる状態だ。
溶接完了し、バフ研磨して組み付け確認。
100時間を超える全工程が終了した。オリジナルに引けをとらない仕上がりではないか。
こうして絶版のスイングアームは復刻された。溜まっているバックオーダーが恐ろしい。
大分のホンダウイングイワオ様から特注の製作依頼です。
10モデルCRF250Rのエキパイ製作ですが
ノーマルがステンレスと鉄のフランジに対してチタニウムとアルミフランジでリプレイスします。
チタンパイプφ35とφ38.1の2種類を使います・
片方に蓋を溶接して砂を詰めます。
この砂詰めが不十分だとパイプが潰れたり、皺が入って不良品になってしまいます。
1台分のパイプ代が1万円くらいしますの無駄にすることはできません。
量産のエキパイは100%機械曲げです。
パイプを潰さないように曲げるためにはR曲げ専用の機械が必要で非常に高額な投資になります。
我社は高額な投資はしません。なぜなら、お客さんの必要数は1本だけだからです。
1本だけ曲げるのでしたら、このように万力と炙りバーナーだけで充分です。
180°曲げですが熟練した手曲げ技術がないと高価な材料を何本も無駄にしてしまうでしょう。
これができないとマフラー屋とは呼べませんね。
取り回しは車両がありませんので、このような治具を作って合わせます。
イワオさんからノーマルのエキパイと取り付け状態の画像を送っていただき、それを元に車体との位置関係がうまくいくようにゲージを作っておきました。
曲げたパイプをつなぎ合わせてノーマル形状のエキパイが出来ました。
フランジはアルミ板をフライス加工で作ったものです。
ホンダのモトクロッサーはHRCのキットパーツが別売りされていますので純正部品はコストダウンの対象なのでしょう。
やっぱり他メーカー並みにチタニウムにしていただかないと私の仕事が増えてしまいます。
【サイドビュー】
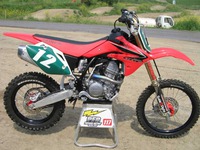
新品のホイールをばらして、リムはアルマイトにハブは塗装で足回りを引き締めて魅せる。
エンジンも下ろしてフレームやリヤサスも塗装する。
やはり、うちのレーサーは黒が純正のカラーだろう。
しかし、プラスチックパーツは本職のデザイナーが作った純正のままがいい。
実は黒と赤の色のコーディネートが最強の色相なのだ。
余計な飾りも不要、ノンスポンサーを強調することが、オリジナルの意気込みを表現する。
要するに、人にやってもらったことに対してあまり価値観を見出していなくて 自分で手間をかけた部分にマシンいじりのロマンを感じているわけだ。
【サイドカバーはずし】
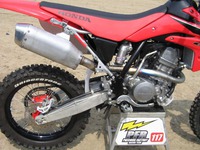
焼け色が変わっていくのも楽しみの一つ。
全体が焼けたら、サンドペーパーで磨いて何度でも新しい焼け色を楽しめる。
一見ノーマル風のサイレンサーは中身とエンドパイプがオリジナルのものに取り換えてある。
シングルのエキゾーストをデュアルに作り変える試みだが、排気音とパワーの出方を変更する目的だ。
アルミのブレーキとチェンジペダルは他機種の純正部品で流用しただけ。
フロントエンジンハンガーはノーマルの高張力鋼板から超ジュラルミンの削り出しに取り換えてある。
【リアフォーク・スプロケット】
150R最大の欠点であるリヤフォークの強度不足を対策した補強リヤフォーク。
7Nー01材で曲げ応力が最大になる箇所の断面積を30%増して対応している。
町工場はメーカー任せにする必要はないのだ。
一見スペシャルのスプロケットはノーマルベースで112個の穴空けをして軽量化した。
ノーマルはなんと、820gも重量があるのだが、570gまで落とした。
しかし、タロンのアルミは270gしかないので2倍の重量だ。(残念)
但し、耐久性は3倍くらい期待できるので、コストパフォーマンスで断然勝っているはずだ。
テスト中の新型構造はマフラー内部で二股に分岐させ、2本のパンチングパイプを通って排気され
る。
ノーマルの開口面積と同等の2つ穴にした場合、約1dB排気音が上がることが分かった。
排気を2列にすることで排気ガスの流速があがるためと思われる。
これがパワー的に有利だということを示しているのだが、あとは、パイプ径の調整をすれば音量のコントロールも可能だ。
とにかく、いつも同じマシンに乗っていたのでは、ライディングそのものの情熱が冷めていってしまうので 常に新しい試みと、ベストコンディションを保つメンテナンスを怠らないことがモトクロスを長く楽しむ秘訣ではないかと思う。
2スト車の車体に4ストエンジンのスワッピング(換装)は何度もやってきた。 しかし今回のスワッピングは今までのとはわけが違う。
これまでのエンジンは旧式の空冷2バルブであったのに対し、これは新型の水冷4バルブだ。 おそらく日本で初めての組み合わせだろう。前後サスペンションはホワイトパワー。リヤはリンクレス。 ブレーキはフォーミュラの対向ピストン。国産には採用されないヨーロッパ製品が目を引く。 画像はエンジンのレイアウトを検討している様子でエンジン位置は決定したがフレームのパイプは繋がっていない。高くなったキャブレターにあわせたエアクリーナーの変更、シリンダーヘッドをかわしたガソリンタンク製作、フレーム中通しの専用エキゾーストパイプetc.難題山積みである。 おそらく実走できるのは夏頃だろう。
この製作計画を聞いて殆どの人は無意味だとか、改造しないでそのまま乗るのが一番いいとか思われるだろう。 実は製作を担当している自分自身も同様に思っていたのだが、製作を諦めさせる説得をしながら、自分の気持ちが完成させて走らせてみたい方向に変化していった。
これを無意味なことと思う人は、マシン選びにどれ程の理由があるだろう。 メーカーのイメージであったりレースで上位を走る機種であったり、バイク店との付き合いであったり。いずれにしても明確な根拠は存在しないはずである。しかも、高額な支払いをして手に入れたマシーンも翌年にはあっさりモデルチェンジされて旧式になってしまう。本当に乗りたいものを決める手段が完全にメーカー任せになっていて、お客さんは踊らされている状態だ。そんな宛がわれたような選択肢では、ただ流行にながされて、他人の真似しかしない日本人の一員になってしまう。
他人と違う方式を試みる精神がこの車両の製作に現れているではないか。 これが完成して走っている姿をみて、どんな乗り味なのか興味を持つ人は多いだろう。しかしその答えは作った者、乗った者にしかわからない領域だ。
無意味だと思う人には一生わからない答えだろう。 そしてこの製作を実現する手段に弊社を選んだ依頼者に満足していただくために腕を振るわなければならない。
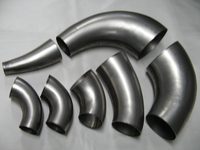
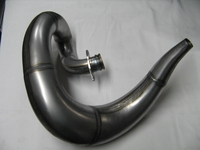
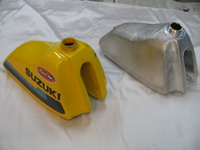
