■ エキゾースト パーツ
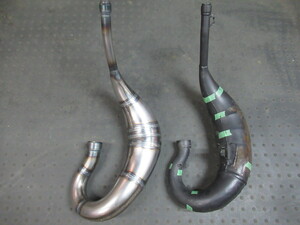
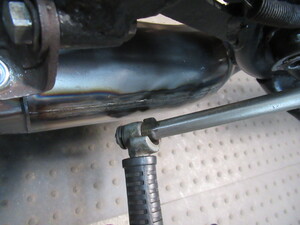
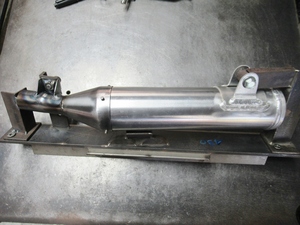
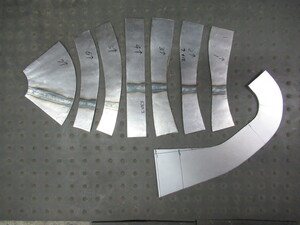
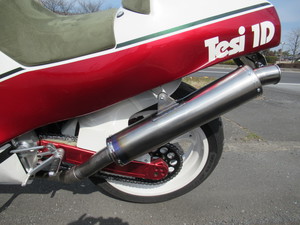
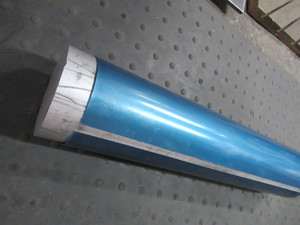
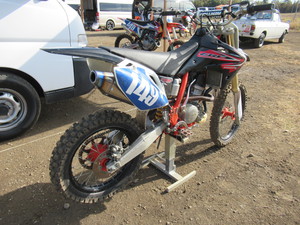
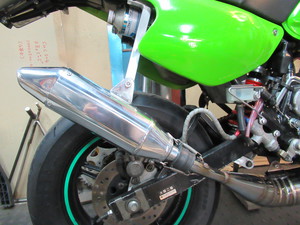
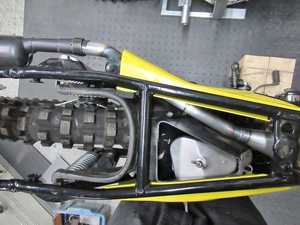
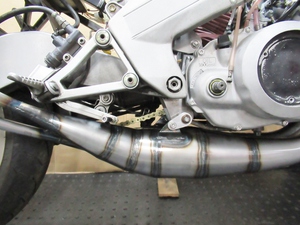
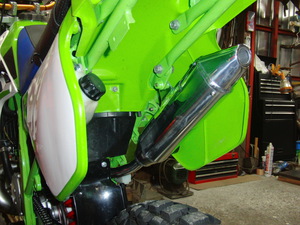
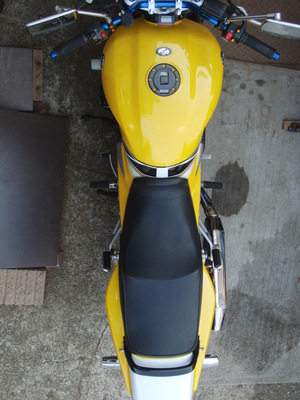
もの忘れの悪い癖で鉄板の在庫を切らしてしまい、取り寄せ中です。
鉄板が無くてはチャンバー作りもできません。材料入荷するまでやっておくことがあります。
CRF150R用のサイレンサーをモデルチェンジします。
2007から作っていた物はチタンパイプを使用していましたからMFJ公認レースは適合でありませんでした。
今年のモデルはMFJ適合を目指してステンレス/アルミを使用し、マンネリ化したデザインを一新して視覚的に闘争心をかきたてるように作ってみました。
実は250用のツインマフラーはシングルマフラーより若干サイズが小さいため専用サイレンサーを作る必要がありました。
そこで150用を作って同じサイズで250のツインマフラーを作るための前段階というわけです。左側は右と対称型でいけるはずです。
断面は平行四辺形です。横幅を増やさず容積をアップさせています。
中身の作り込みは後日やります。
実車取り付け状態もその後で、
一応今のバックオーダーの分から新型マフラーに切り換えていく予定です。
そろそろ材料屋から電話が来ると思うのですが、もう少し進めておきます。
エキパイのジョイントを加工し、マウントブラケットを溶接して、取り付けレイアウト確認します。
全長はノーマル同等ですが、横投影図は大きく見えますね。
リヤビューです。横幅は割とスリムなんです。
中身の構想は出来ていますが加工は、ずっと先になります。
材料屋から鉄板入荷の連絡があったからです。
これから材料取りに行ってチャンバー作りに復帰します。
長期滞留車はあと2台で終わるのですが、430チャンバー10台分なので最後の車両に取り掛かるのが3月後半くらいになるでしょう。
毎日、ご注文や修理依頼が入って参りますが、お引き受けできる状況にありませんので、全て納期未定と返事させていただいております。
長期滞留車集中業務、去年12月から第5弾になります。
今回はワンオフではなく10台ロットの生産になりますので、終了まで当分の間新規ご注文はお引き受けできません。
何故10台かと想像するに、35年前に生産されたCR250(機種コード430)がビンテージMXとしては世界中で最も保有台数が多いらしく、当然純正パーツは絶販で
チャンバーなどという薄板の板金部品は相当腐食して実用に耐えない状態のものが多いと推測します。そこで絶販のチャンバーが新品購入できるとなると、喜ぶビンテージマニアも少なからずおられるのではないかということで複製に挑みました。
販売は全面的にホーリーさんになりますので、個人的に頼まれてもお作りすることはできません。
それはこの商品を企画し、原車提供していただいておりますので、その轍を踏まない方の依頼は430に限らず不可能であることを申しあげておきます。
パイプのレイアウトが一部出来上がってきました。
あと一日くらいで全体が見えてくると思います。
えー、上の状態は昨日昼ころで、次の画像は今日の午前中、歯医者へ行ってから昼前の状態です。
パイプは一通り繋がりましたね。
サイドカバー付けて、構成部品の隙間等チェックして、マウントブラケットやスプリングフックを付ければ完成です。
ワンオフではないので複数作ったときの同一性を検証しなければなりませんが、このあと数個作ってみて比較してチェック項目を決めていきます。
パイプの成形も基本的にハンドワークなので、均一なパイプを作るのは職人の手加減にかかっているところが、一般的な工業製品と違うところです。
従って外国に出回って模倣されようとしても、同じ努力をしなければ出来ないはずなので、作ることのしんどさに耐えられる人間でなければ無理でしょう。
サイドカバー付けてみて焦りました。
隙間ギリギリなんです。
図ったわけではないですが運がいいだけですね。
ノーマルも同じような隙間だったのでパイプ作りの精度が間違っていなかったといえるでしょう。
5個くらい作って形状が安定していることを確認してから、取り付け治具を作成して車体なしで受注生産できる体制にする予定です。
長期滞留車の集中業務が続いております。去年11月から第4弾になります。
空冷エンジンのDT125は以前ノーマルベースのチャンバーを作りましたが、今回は79年型YZ125と同スペックで製作依頼を受けました。
YZスペックでDTに取り付くように専用型作るのですが
当時のYZ125チャンバーは左出しに対してDTは右出しなので対照になっています。
最初は取り付くかどうかわからないので
同等のカーブで作ってみましたが、車体が小さいことと、フレーム中通しのレイアウトが取り回しを困難にしました。
タンク下のクリアランスはこのとおり1センチくらいです。
この位置を下げるためにはエキパイのカーブを大幅変更するしかありません。
今回は走行性能のチェックが主目的だと思いますのでこのままいきます。
フレーム中通しのテールパイプに苦しめられました。
サイレンサーはノーマルパイプがつく位置になっています。
カンチレバーのショックユニットが真ん中にありますので、ショックを避けるカーブが複雑になりました。
全く実績のない組み合わせなので試乗してみます。
インプレッションは元国際田舎B級の私が勤めさせていただきます。
トレール車にレーサーのチャンバーつけただけではレーサーのエンジンにはならないだろうと思っていました。
それはノーマルの最高出力が8000rpmで発生に対してYZは11000rpmで発生すること、カタログ上の馬力は10馬力も差があることから、ポート形状やクランクが別物なのだろうと考えられたからです。
まず、3ヶ月も放置した割りにチョーク引いてキック一発で始動しました。軽く暖気してから走りだしますが、分離給油の混合比が濃いのか白煙を吐き出しながら走ります。一般道では5000rpmくらいで巡航できますので、全くパワー感がありません。6000rpm付近まではノーマルベースの方が力強く、走りやすかったです。
ところが7000rpmを超えた付近から豹変します。8000からレッドゾーンのタコメーターを11000まで一気に振り切りました。この加速でフロントも浮いてきます。相当スピードも出ますし、市街地では危ないでしょう。しかし交通の流れに乗った状態ではパワーバンドに入らず、つまらない特性なので走る場所を選ぶ必要があるでしょう。
ノーマルポートでこの変貌ぶりだとキャブレターもいじっていけばレーサー並みに走ると思いますが、乗りやすさとは別ですから、オーナーの判断に委ねることにします。
上手く研磨できています。
エキパイ類もこのとおり
よーし、つけるぞー!
その前にノーマルマフラー装着して試乗しなければなりません。
元国際田舎B級の私が、試乗インプレッションいたします。
CB400に動力性能を期待するなんてことはナンセンスです。明らかに旧車デザインのこれはCB360Tの雰囲気を現代風にアレンジしたはずなのです。
国内ロードスポーツのお客離れ、特に我々の世代は若い頃CBに乗っていたりするのはちょっと不良で勉強なんか嫌いな少年たちだった。
岩清水ヒロシみたいなガリ勉が乗っているわけがないのだ。
そして大学で勉強したエリートがデザイナーになって単車作ったって、我々世代の気持ちをつかむデザインや音がするものを作れるわけがないのだ。よって新型ロードスポーツに見向きもしないというわけだ。
(単なる懐古主義なだけなんですがね。スポーツ用のやつはなるべく新しいのにのるべきだと思います。)
根本的にCB360TはツインですがCB400はシングルなので乗り味が違うのは当たり前です。
シングルのデュアルエキゾーストですからエキパイは細くてよいわけですが、見た目ツインマフラーのようにしてあります。
ノーマルは3000rpm以下の低速トルクは弱いですが5、6000rpmのパワー感が良好で一般道で非常に乗りやすい特性でしょう。8000rpm以上回しても加速感は一定でパンチが効いていません。ゆっくりと流す程度に乗るのが一番心地よいでしょう。
そしてツインマフラーに交換して最初に気付くことは「音」です。ノーマルの原付みたいな大人しさに比べて明らかに存在を感じる太い音です。しかも爆音ではないので周りに存在をアピールできる調度よい感じです。走りだして低速から開けていきますが、太いマフラーにありがちな低速の落ち込みは感じません。むしろ抵抗が取れた軽い吹け上がりに変わっています。5000rpmからの加速はノーマルより若干速いかなと感じますが、大きな差はありません。同様に乗りやすいフラットなエンジン特性です。前述しましたがブン回して楽しむ必要のないクルマなので、軽くなったエンジンレスポンスと太い音で快適なドライブができると思います。
なんたってリヤビューから車種が特定できそうもないスタイルを楽しめることが最大の売りです。
排気が抜けるようになるとキャブレターのオーダーも違ってきますが、これは走行中に違和感は特にありませんでした。
通常は抜けすぎると全開時や戻したときにアフターバーンが出ます。吸入空気が多くなってガソリンの割合が薄くなるためです。
これは走行中のアフターバーンは起こりませんが回転を上げてからアクセル全閉で少し出るくらいです。エアースクリューを若干閉めるか、スロージェットをワンランク上げる程度で改善するでしょう。
突然ですが、エキスパンションチャンバーという部品はエンジン部品か車体部品のどちらのカテゴリーに入るでしょうか。
動力性能に密接に関わる同部品ですが正解は車体部品です。エンジンの開発はエンジン設計者が担当し、車体の設計は車体専門の担当者という具合に別々に行われます。また製造もエンジン工場ではエキスパンションチャンバーは作りません。車体関係の部品メーカーが製造します。
では、その手法はエンジンの開発はベンチテストで行われ、排気系の諸元はストレート図で表すまでです。そして車体屋によってストレート図に基づいてパイプを曲げて車体に取り付く形状をデザインすることになります。
今回、手巻き製法のチャンバーを製作しますが、これはプレス成形の型を決めるための前工程となるものです。しかし量産用のプレス型をつくる必要がありませんのでワンオフで終了ということになります。
先日寸法計測したチャンバーのストレート図を基にテーパーパイプを作成して取り回しの検討を行います。
パイプは溶接しないで傾きを調節しながらカーブを決めていきます。
取り付ける車体は極秘なのでお見せできません。
作業の進行状況をお知らせする目的だけです。
フレームやラジエターとの隙間がギリギリに設定されていますので、取り回し検討だけで一日掛かりです。
このパイプは全部開いて展開図となります。
これからが製作本番です。
取り掛かるまで気にしていませんでしたが問題が幾つかあることに気付きました。
それは、見本となる写真と預かった車体の仕様が異なること、チャンバー取り付けに必要なラバーマウント、ボルト類、テンションスプリングなどは一切ついてないこと、サイレンサーの取り付け位置も決まっていないなど懸案が続々です。
なんとかパイプが繋ぎ終わったのですが残念なことにテールパイプの傾きがいまいちです。シートレールに対して前下がりに見えます。
低いラジエターの干渉を避けるためチャンバー位置を下げたことが原因です。テールパイプをあと1センチ上げたいと思います。ここで妥協してしまうことは許し難い結果になります。
こだわりの1センチです。
テンションスプリング付いていますが、見本がここでジョイントになっていたため忠実に再現します。
テールパイプがシートレールと同じ傾きに変更できました。
ホンダ純正のラバーマウントは既に廃番で入手できません。ホーリーさんとこで別メーカーの在庫を見繕っていただき、430用テンションスプリングと一緒に送っていただいたことでスムーズに取り付けステーの加工ができました。
サイレンサーは推定84モデルKA4だと思いますが、リヤフレームとのオフセットを決めるため専用カラーをラバーマウントに装着して固定できました。
実車はお見せできませんが、チャンバーはこのとおり完成いたしました。
実に半年遅れの仕事でした。
明日から1ヶ月ほど身柄拘束されますので電話は出られないと思います。急用には対応できませんが用事のある方はメール送信していただければ、終業後に返信いたします。
研磨に出す前にまだまだやることが残っていました。
いつも即興で計画性のない仕事の進め方です。知能が低いのでお許しください。
一旦繋がったパイプをぶった切ってジョイントにしました。
フレーム下のマウントステーを取り付けたらフランジが抜けなくなってしまったためです。
放熱性と軽量化のためアルミフランジを採用していますが、鍍金の電流条件がアルミと鉄では違うため、アルミフランジは外して鍍金する前提ではいたのですが、アンダーマウントのことをすっかり忘れていたのでした。
よって設計変更です。
しかもテンションスプリングのフックを溶接したら、またフランジが通らない始末。悩んだあげく、鍍金後にフランジを入れてから前側フックを溶接することにしました。取り付け位置は車体内側で、ステンレス棒を使うので鍍金上の溶接焼けは少なく、外観は損ねないだろうとの判断です。
アンダーマウントは、このように左右のエキパイを固定するようになっています。
マフラーの振られを考えると、ここを止めないわけにはいかなかったのです。
ノーマルは右1本出しのため、左側にサイレンサーマウントはありません。
ステップブラケット下に自家製ラバーマウントを取り付けしました。
ウーム、魅惑のリヤビュー。
今度こそ加工終了です。
後は研磨屋へ2往復してフックの溶接とグラスウール詰め込んだら排気音が聞けるという段取りです。
年末に途中だったCB400SSマフラーの続きです。
2本出しなのでエンドキャップも2個です。
グラスウール入れるタイプなので消耗したらメンテナンスできるように脱着できるようにします。
抜け止めはM6ボルトを使います。
マフラー装着して左右取り付けバランスを確認します。
オートバイは左右対称ではありません。
L側はサイドスタンドとチェーンがあり
R側はブレーキパネルなのでリヤフォークの形状も非対称です。
2本のマフラーをバランスよく配置するために、一歩引いた位置から眺めないと至近距離ではわからないのです。
理想的な位置が決まりました。
残りはフレーム下のマウントブラケットを取り付ければ加工完了です。
そのあと研磨屋へ持ち込み、クローム鍍金仕上げになります。
研磨屋には2週間ほど預かりになると思いますので、それまでの間次の車両に取り掛かろうと思います。
年明けから毎日、ご注文の電話が掛かっていますが今のところ滞留車の特注部品に集中しておりますので、全て納期未定と返事させていただいております。
突発の修理も予定に影響が出るものは対応できません。
一台一台進めていますので遠くない将来に終わると思いますので、ご予約いただいたお客様は気長にお待ちください。
年末の追い込みです。
左右エキパイの曲げが終わったところです。
これからマフラー部分の形状をデザインします。
完成後はクロームめっき仕上げになります。
今回は二重管にします。
めっきの焼け色を抑える目的ですが
実はエキパイのサイズが排気ポートより大きいのです。
排気の乱流を防止する目的で排気ポートに近いサイズのパイプを挿入しておきます。
マフラーの前側の部分ですが
二重にします。板厚の分、縮小したパイプを挿入しています。
目的は、溶接ビードを研磨によって消してしまうため、排気圧で溶接面が剥離することを防ぐことです。内側のパイプが圧力を受け止めます。
後で4本マフラーの製作が控えているのですが、同じ方式で作ろうと考えているので製造トライを兼ねているわけです。
パイプを仮り止めしてマフラーのレイアウトを検討しています。
年末の大掃除のため一旦中断して、正月明けに続きをやります。
安易に引き受けてしまって、またもや後悔の念に苛まれていますが、引き受けるに至った理由の一つに必要条件がなかったことが挙げられます。コストも制限されていませんし、サーキット走行目的なので音量や排ガスの規制もありません。作り手としては全く自由な要件なので、引き受けやすかったのです。取り掛かるまで日数も長かったので、やり始めてから考えればよかろうと思っておりました。
L型ツインのリヤバンクは後方排気でエキパイ長が極端に短いのです。
ノーマルはマフラーというより箱型チャンバーです。後方排気の容積をチャンバー内の隔壁で距離をかせいで確保していると思われます。
触媒はフロントバンクのエキパイの途中とリヤバンク用はチャンバー内に装着されているのですが、排気効率を上げるためかハニカムをぶち壊して筒抜けにしてありました。
どうやらこの車体のスポーツマフラーが販売されていないか、べらぼうに高額なものしか無いようです。
隔壁によるマフラーの構造はノウハウがないためオーソドックスにパイプの延長で対策しようと考えましたが、ノーマルのマフラーしか取り付けようのないリヤフレームとカウルの形状のため、このような取り回しを余儀なくされました。
これがノーマルのマフラーです。テールカウル下のスペースをいっぱいに使ったデザインです。
マウントはM8ボルト(中央)とM6(前側)2本の3箇所でぶらさがっている形です。
いわゆるマウントブラッケットなるものが無いので、新作マフラーの取り付けに苦労しているところです。
このマフラー単品で重量8.6kg
ライセンスプレートとテールランプをマフラー下に直接取り付ける大胆な構造で合わせて9.6kgになります。
サイレンサーは左右独立したものを連結し、
ジョイントのパイプ2種類と燈火類を取り付ける金具を作りました。
マフラー全体の重量は5.6kgでノーマルより3kgの軽量化になりました。
リヤタイヤエンドから出ないように取り付け位置を決めましたが450マフラー2台分の容積を確保するため、このような大きさになりました。
外側から取り付けボルトにアクセスできない構造なので、取り付け金具の製作に丸二日も費やしてしまいました。
上がってしまったリチウムイオンバッテリーも新品に交換しましたので、明日エンジン始動してみます。
翌日、メインスイッチを入れてセルボタンを押しても、全くセルモーターが回りません。
インジケーターや燈火類は全て正常に動作します。
お客さんにその旨を伝えたら、「持ってくる前からおかしかった」といいます。
「バッテリーあがりかと思っていたがセルモーターが焼きついているかもしれない」とも言われましたので、ここで排気音の確認はできないなと諦めかけていました。
ダメ元でセル始動数回、トライしてみました。
すると1回だけクランクが回転したので、もしかするとOKかもしれないと思い再度トライすると、2回転3回転」と段々回り始めました。5回目くらいにアフターバーンが起きたので確信して、もう1回トライしたら始動できました。
リチウムイオンバッテリーは活性化するのに少し時間が必要らしいです。しばらく電気を流しておくと能力が上がってくる性質です。それとコールドスタートでオイルが固かったことも影響していたと思います。
暖気1分くらいでアクセルあおってみますと、なんとレスポンスのよいエンジンか!ちょい開けで1万瞬時に回ります。音はトルク感ありそうな低音で、思ったほど爆音でないことからサイレンサーの容積が適切であったことが伺えます。ツインエンジンだけどマルチのような吹け上がりです。
延長したリヤバンクのエキパイのはみ出し具合です。カウルの横方向は収まっているのでライディングには影響ないでしょう。
こんなオートバイに比べたら、私の所有車なんてカブみたいなもんです。
スーパーバイクを乗りこなすライダーを尊敬します。私は、このシート片足しか付きません。腕も真っ直ぐ伸ばしてやっとグリップに届きます。
危険なので試乗はやめておきます。
量産部品は必ずロット生産されています。ロットの種類や大きさは製造過程における品質特性によって様々です。量産でロット管理しなければならない理由は、材料ロットや熱処理ロットのように納入や処理条件が同一のグループで区別してトレーサビリティー(履歴追跡)を持たせることによって、あとで不具合が発覚したときに選別することにあります。
不具合の追跡調査が出来ないと対象の製品が分からないので改修コストが莫大になることを防ぐ目的があります。
弊社では生産数が少なく一品ずつハンドワークで加工するために部品の不具合は、加工時点で分かってしまいますのでロット生産することはありません。
普通は注文数は1個なので構成パーツは1台分ずつ作りますが、今回は4個一気に作ります。
これだけ作るのに3日も費やしています。
1日1本製作するのが難しいアルミサイレンサーです。
構成パーツを溶接組み立てしたところです。
部品が揃っていれば連続溶接できるのですが、同じ姿勢を長時間続けることによって血行不良になります。
エコノミークラス症候群という症状ですが、私の場合は肩こりや腰痛になってしまいます。
もう年寄りですね。
溶接完了したらバフ研磨です。夏場と違って体が温まるくらいなので助かります。
研磨は自社製品しかやりません。
お客さんに頼まれても専門の業者さんを紹介するだけです。
ここまで出来れば、グラスウールを詰め込んで組み立てるだけです。
明日の段取りを考えながら発送の準備します。
おまけはCBヨンフォア専門店シオハウスさんからお借りしたVMXマガジンから
ジム・ワイナートとトニー・ディスティファーノの接戦です。
トニーの顎にジムの左グリップが入っていますね。
トニーの右ブーツはジムのフロントフォークに引っかかっています。
ものすごい勝負への執念です。安全運転至上主義の私は見習いたいです。
9月一杯まで非常に立て込んでいる状況ですが、電話1本でマフラー1本作ることになりました。
9月1日にJNCCが月山で開催されるのでエントリーしたというので遅くとも29日迄に完成させなくてはなりません。
道なき道を走るエンデューロなので上手いライダーでも転倒のリスクは付きまといます。
レーサーのマフラーは軽量化も考えてチタンパイプを使ったりしますが、今回はステンレスです。
アルミの筒は同じですが、ミドルパイプの強度がステンレスパイプの方が上なので転倒による影響をなるべく抑える目的であります。
重量はチタン製と比較して500gくらい増えますが走行性能には影響ないでしょう。
依頼者は元ワークスライダーの大塚忠和選手ですが、私とはノービスから国際B級まで走った年代がカブっていますので、同年代のトップライダーからの呪縛にかかっていると思われます。別の年代のトップライダーですと観客としてしか見ていないので、特に意識はしていません。
それから、大塚選手はオートマチックのRC250Mを走らせて鈴鹿サーキットで宗一郎さんの前で優勝した人ですから他のライダーとは違う意味合いを持っています。優勝直後に管制塔に呼ばれて宗一郎さんと弁当食べたライダーは彼1人だけです。私ごときが彼の頼みを断れるわけありません。
製作は間に合ったのですが、グラスウールがまだ入庫しません。ギリギリの日程なのでセッティングする時間もないでしょう。
現在違うマフラーが付いてますが、音量検査が難しいので新品頼まれたのでした。
ウエポンで聞いたのですが彼のマシンは月山終わったら売却するらしいので、突貫で作ったマフラーも一回きりで終了かもしれません。んー残念
大塚選手に電話したら、月山は都合で出られないそうで、次の糸魚川から出場ということでした。私、ビビリまくりで損してますね。マシンは今売っても、シーズンオフでも金額は変わらないということで、今シーズン一杯使っていただけそうです。
ようやくできました。サイドカバーとリヤフェンダーが一体になった独特のデザインのため、サイレンサーの位置決めをちょっと考えておりました。
形状はこのとおり、モトクロッサーと同様にヘキサゴンタイプです。
公道仕様のためディフューザーを追加してあります。
クローズドコースを走るときはディフューザー外してフルパワーにするとより楽しめるでしょう。
実はノーマルサイレンサーの出口には蓋が溶接されていて排気の抵抗になっていたため、改造はせずに、新作にしました。
重量はノーマル2.8kgに対して2kgに仕上がりましたが容量はアップしていますので、騒音低めでパワーも向上しているでしょう。
セル付きなのですが、バッテリー上がりで回りません。
しかし、チョーク引いてキック一発で始動しました。ノーマルだと、始動性が悪く長くセルを回し続けないと始動しずらいと、オーナーが言っておられましたので、始動性も改善されたようすです。
音量は・・・明らかに静かなので計測するまでもありませんので、やめます。
07モデルで生産終了したCR85ですから、弊社ラインナップ品は最後に作ってから一年以上経ちますのでCRチャンバーの製作も終了したかと思っていました。
注文数は2台分で、1台は日本でもう1台はイタリヤだそうです。
3月に頼まれたのがようやくできたのですが引き渡し方法が知らされておらず、このまま在庫にしてあります。
フィレンツェ在住の日本人ライダーに使っていただく予定ですが、お父さんの仕事の都合かと思いますが、羨ましいような環境でMXができているようです。現地のキッズレースの動画もメール添付していただいたので観てみましょう。
'>少なくとも関東にはこんなコース存在しませんね。日本の国土の90%は山なんですから、もっとマウンテンコースがあってもよいと思うのですが、難しい問題です。アップダウンもいいですがコース幅も申し分ありません。何といってもスタートフルグリッドというのがよいです。やっぱりMXはこうでないと。
エキパイの鍍金が仕上がりましたので、マフラー製作の続きです。
今日はマフラーのジョイント部分とマウントステー作りに取り掛かります。
見本は量産品ですから、全て金型を用いてプレス成型により作られたものです。
量産は少なくとも千個ロットの生産だったでしょう。マウントブラケットなどは下請けのプレス工場などに外注して大量生産して安価に作られたものです。
しかし、当方には金型などありません。見本の形状を真似て成形するしかありません。充分な予算をいただいてあれば安心して立派なものを作れるのですが大概の部品は製作に費やした時間分の全てを請求するわけにはまいりません。それは、必要な生産設備が無い上に初めて成形する部品であるために、長時間を要するためです。
これはジョイント部分ですが、非常に凝った形状であります。
ボルトを差し込む部分が袋状になっており、左右で4個のフクロを作って溶接で取り付けしてありますが、この部分だけで半日費やしています。
これができれば、エキパイにマフラーを差し込んで、位置決めに掛かれます。
メガホンの溶接ビードは全て消してあります。
溶接のまま研磨屋に出しますと、ピンホールやハンマー痕などが残ってしまって、鍍金の仕上がりに影響してしまうため、研磨の下地はこちらで整えておかなければなりません。
研磨は全てお任せでは、上手く仕上がってこないことが分りました。
ちょっとユニークな形状のマウントブラケットです。
上は見本ですが、なるべくノーマルのデザインを崩さないように真似ています。
締め付け面の凹ましが必要なので、イレギュラーな方法で鉄板を成形してみました。
鉄板はなかなか、言うことを聞いてくれません。
なんとかマウントブラケットの成形ができたので、左右マフラーの取り付け位置を確認しながら溶接しました。
あとはエンジン下側に付けるマウントステーが残っていますが、今日はここまで。
明日、最後のステー取り付けを行って研磨屋に持っていく段取りが整うはずです。
日付が変わって、エンジン下部に取りつけるマウントステーを作って溶接しました。
2枚合わせのステーですが、これも純正になるべく似せて作ってあります。
純正に似せる理由は、それ単品で見るとオリジナルだと思わせるようにしなければならないからです。
復刻されない希少なパーツを新品で再現するということは、旧車の維持には不可欠なことで、商業的に利益を得る目的の「偽物ブランド」とは全く次元の違う話だと思います。
オリジナルと再現品を並べてみます。
B級マフラーと思いますが、大体同じ形状に出来ているでしょう。
鍍金が仕上がってきて、ピカピカになれば、素人さんならどちらが本物か見分けがつかないと思います。
これで私の作業は終わり、研磨屋に持っていってカネを払ってくるだけです。
ここまでエキパイと合わせて10日ほど掛かりましたが、一段落ということで会社なんかだと祝杯を上げたりするでしょうが、私にはあのような発酵した水など飲んだら気持ち悪くなってしまうので祝杯は上げません。そのかわり、気持ちよくなる音楽でも聴くとしましょう。
スパイロ・ジャイラのモーニングダンス。ものすごく爽やかな気分になります。寒気が来ていますので気分だけでもトロピカルでいきましょう!サンキュー、Mrベッケンスタイン(SAX)
'>1979年リリースの楽曲ですから、34年も経つのですね。カセットテープが擦り切れるほど聴いていましたが、何年経ってもエエモンはエエ!
9月のもてぎでお預かりしたCB92のマフラーに着手です。オーナーの沖さんは小樽在住ですが、1月に群馬のスキー場へ来られる情報をお聞きしていたのに間に合いませんでした。次回は4月のイベントで埼玉へ来られるそうなので、猶予ができました。今から取りかかれば充分間に合うでしょう。
完全オリジナルのCB92です。保管には細心の注意を配ります。
何年か前から北野元選手が浅間火山レースで優勝したマシンを入手してレストア中であることを聞いていましたので、2輪史に関る大事な仕事であると思います。
北野さんは関東では有名で、4輪のレースドライバーに転向して、板橋の川越街道沿いにあったロードレースの宋利光さんの店「アパッチ」の隣でタイヤショップを営んでおられました。
託されたマフラー一式ですが、図面もありませんので、この現物を見本に同型のものを作らねばなりません。
具体的にマジマジと眺めてみると型物が随所に使われていて、ハンドワークで再現するのが難しいように思われます。
しかし、私には19年も何の道具も持たないで、「無いものは造ればよい」という信念でやってきた経験があります。
緩いカーブを描いたエキパイは3次元に曲がっているのが分ります。
メーカーさんは機械ベンダーで曲げRと角度を設定して曲げていますが、私には曲げ機械はありません。手曲げで再現するには職人技を発揮する必要があるでしょう。
マフラーのマウントステー部分の構成パーツが意外と多いことに気づきました。
おそらくこの部分の作り込みが半分くらいのウエートを占めると思います。
2枚の板の接合部はスポット溶接が用いられていますが、スポット溶接機もありません。この部分はプラグ溶接かTIG溶接で取り付けさせていただきますのでお許しください。
では製作の進行状況は随時アップすることにいたします。
2輪史について、何のことだか分らない人も多いかもしれません。最近のことだけ見ていると全体像は見えてきませんが、MX、ロードレース、ストリート、クラシック、改造バイク、一通りのカテゴリーを掻い摘んで見てきました。2輪車という乗り物は、およそ100年前の原点から始まり、研究開発が進んで新材料、新製法、新機構が世の中にリリースされ、お金を払えば誰でも堪能できる便利な時代になったと思っています。
しかし、この先100年同じように開発が進んでいくとは思えません。それは資源や環境の問題であったり人間の欲求の矛先であったり、残る部分と衰退していく部分が当然でてくるでしょう。今の繁栄は期間限定の楽しみと捉えてよいかもしれません。そのことを考えると、一見時代遅れに見えるようなことに魅力や価値観を見出していく懐古主義を営んでいくために手作り製法も、残された人生を豊かに(お金じゃないですよ)過ごしていくために有意義なことだと思って働いています。
通常はテーパーに削った鉄棒に鉄板を巻きつけながら作りますが、これは端材も含めて1m以上の長さがありますので巻いて作るのは難しいと考え、水押しで膨らますことにしました。
2枚の鉄板を展開図に従って切断し、溶接で張り合わせます。
今回は厚さ1mmの鉄板を使用しますが、成型後に溶接ビードは研磨して消してしまうため、通常より溶け込みを深く溶接しておきます。
製品の長さが77mmありますので、CB92のシートより少し高いです。
マフラーの長さは排気の脈動を利用して燃焼室の充填効率を高める効果がありますので、ノーマル寸法を守る必要があります。
旧車の場合はオリジナルに忠実な外観も必要なので、自分の意思は入れず同じように成型することに没頭するだけです。
メガホンのエンド部分にはテーパーリングを溶接します。後で研磨して溶接ビードは消します。
テーパー状の絞りは排気の抜け過ぎを抑え、反射を起こすための形状です。
50年前からこのようなチューニングの技法が確立されていたのですね。
メガホンの加工はここで一旦停止です。先にエキパイの製作に掛からねばなりません。
その理由は、クローム鍍金仕上げ によってパイプジョイント部の外径が大きくなってマフラーが差し込めなくなるためです。
ラインナップ品のチャンバーなどはテールパイプのジョイント部をマスキングして、鍍金が付かないようにして対応していますが、CB92のエキパイは端まで鍍金されていますので、鍍金後の外径寸法にあわせてマフラージョイントを加工する段取りになります。
先ずは見本のエキパイから曲げゲージを作ります。左右対称ですが、3次元曲げなので両方のゲージが必要です。
炙り加減と力を入れるタイミングは100%勘だけが頼りの手曲げです。
複合Rの距離が近いため、このカーブを成型するには高級な機械ベンダーが必要でしょう。
パーツメーカーさんならCNC加工機により高精度な仕上がりを実現します、というところですが、ここでは無縁の世界です。
先日作っておいたメガホンマフラーを仮止めして左右のバランスを見ます。
マフラーの位置が問題なければ、エキパイの加工は完了です。
このあとエキパイだけ鍍金処理に廻りますので、それまでマフラーの加工は中断します。
次の仕事が控えておりますので、続編は2週間後ということで。
ようやくセンター出しマフラーの音量計測です。
先日、マフラー完成後にエンジン始動しようとして失敗しました。
冷間時の初期始動性が良くないエンジンだと思いました。
考えられる要因はバッテリーの過放電、長くエンジン始動しないで放置しておくと漏電して電圧が下がってしまう現象。
もう一つはこのマシン特有ですが、ガソリンタンクの絶縁が悪く、フレームとタンクが金属接触しているため放電して引火することを恐れました。そのため、タンクを外して作業しようとしましたが、燃料ホースのカプラーが外しにくく、壊しても困ると思ってガソリンを抜いてしまいました。エンジン始動時にはガソリン給油して行いましたが、必要な燃圧に達していなかったかもしれません。
真相はわかりませんが、走行する必要はないので別の新品バッテリーを購入して電圧確認してから再トライしましたが、同様に始動せずバッテリーが弱ってきたので中止して、自家用車のエンジンをかけてブースターケーブル繋いでようやく始動できました。
この車両はアンチグラビティー製のリン酸鉄リチウムイオンバッテリーが装着されています。
同じ性能のユアサと比べると体積で3分の1、重量が4分の1くらい違いますので、ユアサは取り付きませんがブースターで始動するために使用しました。
ブースターで充電しながらセルを回せるので、今度は簡単に始動できました。
そして、排気音は
車検は近接騒音で、最高出力回転数の50%に保持して計測するので
4500rpmで80dBという静かさ、10000rpmでも90dBくらいなので数値は余裕で合格です。
念のためマフラー出口にディフューザーを付けていますが、外しても2dBほど上がるだけなので、好みに応じて外しても問題ないでしょう。
公道仕様のためテールランプとライセンスプレートのステーが必要です。
最もシンプルな取り付けをデザインしました。
アルミのリヤフレームにボルトオンでステンレス棒のステーを作ってみました。
2?のアルミ板をベースにテールランプとライセンスプレートが取り付くはずですが私の仕事はここまで。あとはオートバイ屋さんにお引き渡しとなります。
大晦日にジョイントは完了していましたが、過労のためか正月早々に寝込んでしまい、3日から再開です。
しかし、マフラーが固定されているわけではありませんので、リヤフレームに取り付けのためのステーを新設します。
リヤバンクのエキパイはフロントバンクのエキパイと等長とするため2回Uターンして長さを稼いでいます。
アルミとチタンの複合で、総重量2.2kgまるでレーサー並みです。
カウルをセットしてマフラーとの整列を確認してみます。
タイヤセンターとマフラーの芯を合わせるようにステーの位置決めをします。
FRP製カウルの位置は必ずしも車体中心と合っているわけではありません。取り付け穴位置を加工して中心になるように変更します。
ここまで来れば、あと一息なのですが、マフラーのラバーマウントのための部品を発注しなければなりません。
来週まで部品屋が動きませんので、完成は来週に持ち越しですが、残りの加工は明日一日で終了です。
マフラーのマウントが完了したのでリヤクッションフルボトムさせて、タイヤクリアランスを確認します。ショックのストロークを変更して対応しました。
ノーマルはオフオード車なのでロングストロークですが、オンロードならこれくらいのストロークで充分な気がします。
マフラー取り付け業務完了しましたので、音量測定のためエンジン始動を試みましたが、残念ながらバッテリー電圧不足で始動できず、バッテリーチャージャーも持ち合わせておりませんので、後日電圧を復活させてトライしたいと思います。
これは公道走行可能なレベルに仕上げる目的なので、ライセンスプレートとテールランプのマウントステーも作らなければなりません。
あと少しですがリヤフレームに留められるスペースが殆どないので悩んでおります。
なかなかはかどりませんので、小出しにします。
センター出しのマフラーは、こんな形状にします。
タイヤクリアランスの関係で横置きにします。
これが出来るとリヤフレームの変更内容が決まります。
年内に2つのエキパイの取り回しを行いますので新年早々にジョイント完了するはずです。
正月も遊ばないで仕事、仕事。
リヤショックのスプリングコンプレッサーも自作です。
レーサーのショックはスプリングアジャスターを緩めれば簡単にスプリングが外せるので特殊工具は必要ありませんが、これはアジャスターを全部緩めてもはずれません。
特殊工具は工具店で購入できますが、私は買ってきません。自作にこだわります。
その理由はコスト削減のためです。「ワンオフのわりに価格が安いですね」と言われることがありますが、こういうことをして出費を抑えているんです。
これの場合は、充分元を取ったシャコ万とスクラップの鋼材で総額、数百円でしょう。高い特殊工具を買ってくる気はありません。他にもエンジンメンテナンスならケースプーラーやクランクシャフトインストーラーなど全部自作です。コストが安いだけでなく、用途に合わせて作っているので使い勝手がいいのです。
ようやく取り掛かる時期がきました、SXV550。アプリリアのVツインです。本当はモタード車ですが、依頼されたカスタム屋さんでロードタイプにモディファイされています。
実は、電話でマフラー製作の話をいただいたときは、車両の状態が分らず、お引き受けに至りませんでした。
詳細が不明な状態で、出来ますとは返事ができないからです。
そこで、電話とメールのやり取りで段々と状況が見えてきました。
リヤサスのリンクを変更して車高が下げられていること、ノーマルのマフラーが取り付かなくなっていること、リヤバンクのエキパイが短く延長しなければならないことなど。
ちょっと厄介なことになりそうだったことと仕事も2ヶ月ほど溜まっていて、係っているとますます遅れてしまうことになると思い、受託の返事を保留していました。
そうすると、無理な部分を理解していただいたようで、やり易いようにリヤ廻りのジオメトリーを変更しても構わないということで了承いただき、車両持込みしていただくことになりました。年内に完了することは不可能なので、材料の手配はしておいて来年に持ち越しということになります。
モタード車のノーマルマフラーはフェンダーを兼ねた箱型のサイレンサーに2本のエキパイが差し込まれた形状です。
リヤショックのスプリングを外してサスをフルボトムさせて、スペースの確認です。リンクで車高下げた場合は、車高が下がった位置からフルストロークするのでタイヤとフェンダーのスペースが無くなってきます。
この隙間にセンター出しのマフラーを取り付けるなどということは不可能なことがわかります。リヤフレームを改造してマフラーのスペースを確保することから掛かります。
来年の初物になると思いますが、続きはまた来年ということで。
ようやく2台目のNSR250のチャンバー作りです。製作実績がありませんので、毎回悩むところですが、今回はお客さんの要望で右二本出しのサイレンサーが特徴です。
89モデルと思われますが外装部品は既に廃盤になっています。フルカウルは全塗装したのかと思っていましたが、じつはグラスファイバーで復刻したものでした。
ノーマルはインジェクション成型なので、裏地の肌が違うことで気がつきましたが、生産されない旧車のために、カウリングを少量生産するメーカーがあるようです。
引き締まったスタイリングが好感をもてますね。
アンダーカウル装着のためにチャンバーの取り回しが複雑になります。
90度V型のリヤバンクは右出しに、フロントバンクはUターンして左出しという変則カーブを描きます。
通常左向きにひねったコンバージェントコーンを右向きに変更して右出しのテールパイプに繋げています。元々センタースタンドが無く、リヤサスのリンク位置も問題なく、後ろ側の取り回しは自然な形にできました。
まだまだ年内はワンオフの製作が続きます。当分の間、工房に篭って仕事していますので春ころまで掛かります。電話も出られないと思いますがご了承ください。
息抜きは必要なので、今日の音楽ネタはコテコテのジャズにロックを融合させて聴きやすい音楽を作ったフュージョン界の功労者、デイブ・グルーシンの立ち上げた演奏集団GRP AllStarsからマウントダンスです。自分はデイブ・グルーシンの演奏を観るのはこれが始めてで感動しました。ギターの神様リー・リトナーも参加されています。この楽曲聴いていると80年代が蘇ってきます。
2スト全盛期は老舗のチャンバー屋さんが沢山ありましたので、選り取りだったと思います。2スト全廃の今では入手困難になってしまったようで、今頃になって初めて作ることになりましたNSR250用チャンバーです。
左右非対称のチャンバーなので2種類の型を作らなければなりません。
先ずは90度V型ツインの前バンクの方から型を決めてレイアウト検討します。
ノーマルのアンダーカウル装着のため、エキパイのカーブもノーマル同様にしないと収まらなくなります。
その結果、オフロード車のチャンバーよりタイトな曲げカーブが必要になります。
前バンク取り付け状態ですが、このようにクネクネ曲がっています。
このあと、後バンクからのエキパイのレイアウトを検討するのですが、ラジエターとシリンダーの隙間を通って右側に出てくることになります。
エキパイのクロスは過去最高の難易度となるでしょうが、長年の経験で決めていきたいと思います。
後バンクのエキパイは前にラジエター、下に前バンクのエキパイが干渉するので狭い隙間を数ミリの隙間を空けて通っていきます。
これでクロス部分の取り回しが完了しましたが、テールパイプとサイレンサー2本の製作が残っていますので完成は来週に持ち越しということで、今週はここまで。
パイプ本体が出来たとしても完了には程遠いです。
サイレンサー2本作ってテールパイプの曲げカーブを決めて、サイレンサーの取り付けバランスを見なければなりません。
最初は溶接されていないパイプを手で持って取り付けバランスを確認しますが、離れて見ることができないので、目見当だけが頼りです。
接合部にマーキングして溶接して再度取り付けて確認という作業を繰り返します。しかもアンダーカウルも脱着しながらということで
作業時間は刻一刻と過ぎていきますので、お時間の約束をしても守れたためしがありません。
ひとまず取り付け完了しました。カウル装着すると全部隠れてしまいますので、この状態で撮影です。
今回も初めて作るチャンバーでしたが、製作するのに必要な図面やモデルも無しで白紙の状態から取りかかるのです。
しかも1週間くらいで仕上げないと商売になりません。他の仕事全部止めていますからね。
今回低い姿勢での作業が多く、無理な体位で腰痛が始まってしまったことが余計な悩みです。体の老化現象が確実に忍び寄っています。あと幾年続けられるか体力だけが頼りの仕事です。
先日、地域の盆踊り大会があって、今年役員をさせられていますので設営やら模擬店の手伝いにいってきました。このへんはホンダOBが多く居住されている場所で、定年になったOBの話を少し聞きました。
早期退社で退職金と厚生年金をもらって、金銭的には余裕がありそうですが、退職後の生活のことや在職中の職務の辛さなどを考えさせられ、どうしても、自分の立場と比較してしまうのは僻みというものでしょうか。
シングルで最大排気量はDR800だと記憶していますが、これは2番目に大きいやつです。車体も大柄でいかにも外人向けな作りです。キックスターターもありません、セル始動なのが唯一の救いです。フルエキゾースト製作の依頼をお引き受けしたのですが、オーナーの境遇を聞かされて大変恐縮して作業に取り掛かっています。
それは、ご自宅が福島の強制避難区域にあるということ。避難先の社員寮に他のオートバイと一緒に移住しておられて、200km以上も自走して我社に車両もってきていただきました。
それを聞いたときに心を打たれました。原発事故がなければ自宅でそのまま好きなオートバイを大事にしながら過ごせていられたはずなのに、こんなことになってしまって・・・。幸い職場は再開されて経済活動はできていらっしゃるようですが、オートバイのことをあきらめないで乗り続けておられることに喜びを感じます。おそらく、大変多くのオートバイフリークが原発の影響を受けて、好きなことを諦めてしまったんじゃないかと察していたところです。
せっかく日本の原発がゼロになったというのに大飯原発は再稼動されるということです。高度成長期以降の日本の経済成長は原発を含めた電力がなければ不可能だったでしょう。もちろんこの経済を維持しなければ、社会保障や高齢者医療の財源が捻出できないということも充分理解できます。
しかし、原発再開に導く政策を決めているのは都市部の便利で快適な生活を営んでいる富裕層であろうということ、こういう人たちは、もう少し田舎に引っ越されて質素な生活を経験した方がいいと思いますよ。浪費している一部の人たちの幸福という名のもとに生活レベルを支えるために大きな犠牲を払ってしまった。なにより、処理困難な核廃棄物を作りつづけ、使用済み燃料プールももうすぐ満杯になってしまうというのに、最終処分の方針も全くきまっていないまま、この経済活動を続けるという動きは確実に将来、大きな災難が降りかかってくることを意味しています。何の反省も改善もみられない、事故の収束も止まったまま、国家のリーダーたちの采配に落胆するばかりです。
現実は待ったなしです。先送りはできません。
結構仕事溜まっていますので、長くお待ちいただいているお客さんの希望に応えるために働き続けます。
XR650のデュアルエキゾーストは複雑な曲げカーブが必要なのでSUS304のパイプをこれだけの数曲げて、取り回しします。
SUS304は耐熱合金なので800℃くらい加熱しても強度があまり変わりません。手首の靭帯が切れてしまいそうな力を込めて曲げなくてはなりません。
R曲げ9箇所になります。
溶接つなぎ終わりました。
クロスしたエキパイの製作は通常の1本ものと比べると加工時間が3倍になります。
ところが費用も3倍にはできないというところがこのエキパイの難しいところです。
材料代は現金で仕入れておりますので削減できませんが、人件費を削減して対応しております。
ヒートガードも頼まれましたのでアルミ板金で製作しました。
最初はカーボンファイバーで、と言われたのですが我社では樹脂は扱っていませんので外注することになりますが、おそらくマフラー代よりも高額なヒートガードが出来上がってくると思いますので予算オーバーになります。
そういうわけで、これでしたら半日あれば充分なので迷わず実行です。
フルエキゾースト完成です。
エンジン始動してみましたが、さすがビッグシングル!セルモーターでも始動にはコツがいる感じです。ホットスターターは付いていないCVタイプのキャブです。
たぶんキックスターターだとこのマシン嫌いになるでしょう。
チョークとアクセルチョイ開けの併用で目覚めました。バッテリーの電圧が命ですね。暖気運転中、エンジンストップして始動不能になって焦りましたが、10Aヒューズが切れていました。結構な発電能力を持っているようです。
ブローバイガス還元装置は取り外し大気開放にしましたのでエンジン回転が軽くなった気がします。ブリザーチューブから排出される圧力がエンジン内部に掛かっていることを考えると馬鹿にできないポンピングロスなのだと思いました。ノーマルの還元装置はブローバイガスをキャッチタンクを介してインテークに戻すしくみになっています。すなわち、エンジンの吸入負圧でケース内の圧力を抜くと同時に未燃焼ガスを再吸入して燃やすという働きをします。この装置を取り外したメリットはブローバイガスに含まれたオイルミストなどをインテークに吸引せずインテーク通路をクリーンに保つということです。万が一装置が故障してもケース内の圧力が上昇してしまうこともありません。
マン島の公道レースについて否定的な意見の人もおられるようですが、正しい論理で批判されているということを理解しながら、現代のモータースポーツと交通社会の係わりについて思うことがあります。
批判の要点は競争社会をベースに市場原理主義の縮図としてライダーや観客の命を軽視した観光産業と言われています。これはマン島TTレースの百年間に224名の死亡者を出しても懲りもせず、毎年危険な公道レースを続け、犠牲になった人は自己責任の名の下に葬り勝者を賛美しているどうしようもない人間の集まりと批評されているわけです。
そのように採られてもしょうがない一面はあると思いますが、これは合法で運営されている以上、日本の道路で交通違反をして事故を起こしている人たちからは批判を受ける筋合いは無いでしょう。私個人的には2輪の運転技術に公道やレース場の境界は無いと思っています。同じ技術をベースに道路に合わせて運転しているだけです。運転技術が高いということはレースの成績が良いことと、公道で安全に運転できるということに相関があるはずです。
日本では毎年1万人位、自動車事故で死亡しているらしいですが、自動車業界こそ競争社会、市場原理主義の象徴と言え、一部の顧客からの危険運転により交通事故が起きている現状をわすれてはなりません。少なくともモータースポーツに参加している人は運転技術の向上を目指して練習しているわけで、練習もしてないで道路で危険な運転をされては危なくて仕方ありません。
クローズドコースにおける技術より公道レースにおける技術の方が実際の交通の流れに入ったときに有効だと思います。実際の生活道路で限界の走行ができるのですから、法廷スピードで走ったときの安全性はレースに参加してないドライバーとは比較にならないでしょう。唯、レーサーだって人間ですから僅かなミスや疲労が重なって、レース中に事故が起きてしまったので、これを批判するよりレース経験も無いのにスピードを出す一般ドライバーに対して指導したほうが効果的というものです。
道路を走行中によく見かけますが、安全な車間距離をとって走行しているのに、周りのクルマよりスピードを出して割り込んでくる輩がいます。衝突しないのは周囲の運転者が避けてくれているだけということを理解する必要があるでしょう。上手い人は他人に不安を与える運転はしないはずです。
本題から離れてしまいましたが、公道バージョンのCRF250Xにレーサー用のサイレンサーを取り付けてみました。
これはお客さんの依頼でエンデューロレースに出るために作ったサイレンサーで、250Xのノーマルより軽いこととパワーも上がっているはずです。
250Xのサイレンサーは米国EPA(環境保護庁)の認定を取っていますが、排気ガスの浄化より、枯れ草に火炎が飛ばないためのスパークアレスターを装備していますのでレーサー用より重いのは仕方ありません。
国内のエンデューロのスパークアレスターは義務付けられていませんので問題ないでしょう。
トレールバイク以外ではMXレーサー用のチャンバーとしては最も長く作り続けている車種YZ85です。80cc時代も含めると17年になります。
現在使用している組み立て治具に年式が書いてあるのですが、02年とありますので10年間同じ型で毎年製作してきたということです。本体のエンジンも01年あたりで、クランクケースやクランクシャフトが一新されましたが、そのまま開発は止まっているようです。
YZ85は80時代に比べれば低速トルクもありますが、それでも排気デバイスを持った他メーカーの車種に比べると高回転高出力なエンジン特性です。
このチャンバーのコンセプトは低速から中高速へ繋がるパワーの上昇をフラット化して乗りやすくしてあります。ノーマルでも高回転をキープできる技量のライダーなら速く走れますが、低速コーナーが続いたり、スリッピーな路面では神経質にならざるを得ないでしょう。そういう部分で乗り手を助けてくれるはずです。
サイレンサーにおいては排気抵抗を軽減して軽いエンジンレスポンスを目指しつつ騒音もノーマル以下を実現しました。
これは車両が今でも新車販売されていることもありますが、若年層を中心に扱いやすさが評価されていることで製造が継続できていると考えられます。大体年間10台ほどの注文がありますが、仮にまとめて作るとすると20日くらいで出来ます。1ヶ月に満たない仕事量ですが、10年間継続してきているということで、この企画が間違っていなかったものと確信しています。
4ストのYZ150Fの噂もありましたが、欧米で需要が見込めないと判断されたとも言われていますが、メーカーとしてもミニバイクに250クラスと同等のコストをかけて販売するという暴挙にでる必要もないという冷静な判断の結果です。
しかし、この先10年、20年と同じエンジンを作り続けるとは思えません。時期モデルがどのように変化していくかが興味を持たれるところですが、おそらく20年後私が生きている保証がありませんので、やるなら早くやっていただけませんかヤマハさん。
世間は大型連休中ですが、予定の業務が終了していない弊社はエンドレスで進行中です。
1ヶ月近くお預かりしているマシンのチャンバー製作に着手しているところですが、予想に反して手強いです。
TZR250の後期モデル、89年から3年しか生産されなかった前方吸気、後方排気という珍しいレイアウトのエンジン。
91年からV型となるため並列2気筒としては最後のモデルとなります。
しかし、このレイアウトはメリットとデメリットがあって総合的にはどうなのか、いろいろ乗り込んだ人しか分らないと思いますが、私個人的には面白いですね。
何で他の機種ではこういうレイアウトが採用されなかったのか興味深いところがあります。
クランクケース吸入ですから、キャブレターが後ろでも前でも吸気量は同じですが、通常レイアウトではキャブレター周りが熱くなってしまいますが、前方なら冷やされますから、フレッシュなエアーが吸入され充填効率が上げられるでしょう。排気管も後ろ向きの排気ポートからストレートに排気され抵抗も少ないでしょう。
チャンバーの寸法は依頼者からエクセルで作図したものをメール送信していただき、それに従って製作するだけです。ところが、真っ直ぐなパイプを作るわけではありませんので微妙なカーブを作ることで難航しています。
左右のエキパイを成型して口元フランジを固定してみると、これではパイプの位置が高すぎます。シートの下が近くて配線などが焼けてしまうことになりそうなので、やり直しです。ここまで2日かかっていますが、惜しげもなく廃却です。
即効で少し下向きに変えたカーブのエキパイ2本を作成して続行です。
このようなことを繰り返していますので予定どおり業務が進まないということになります。
納期は約束しても無駄ということです。
初めて作るものはどうしても時間がかかりますが完成したときの喜びも既成品とは違うものがあるのです。
うーむ、官能的です。
リヤストレートとは名ばかりで、クネクネ曲がってないと、サブフレームやサイドカバーと干渉してしまうので、必然的なカーブを描いています。
これからテールパイプとサイレンサー2本作らなければ完成しません。
あと20時間くらいでしょうか、もうひと頑張りします。
サイレンサー2本、リヤカウルに空いた穴から突き出しています。
4ストのセンター出しは、このモデルから発展したと言えます。センターはリヤタイヤが上がってきますので、チャンバーは両側に張り出した形状にしないと当たります。
サイドカバー付けると全部隠れて見えなくなりますのでストリップ状態だとこのようになります。
これでオーナーの設計されたチャンバースペックで製作が完了しました。
GW+3日の工程費やしましたので、この後も過密スケジュールで進行していきます。
ワンオフ製作のチャンバーを希望されるお客さんは次のことに、ご注意ください。
製作したいチャンバーの寸法図、または見本が無い場合はお引き受けできません。チャンバーの諸元はエンジンの仕様と密接な関係がありますので、車種毎に専用設計になっています。寸法図が提示されない場合は新規に設計しなければなりませんが、経験の無い車種のチャンバーをゼロから製作するとなると相当な試作とテストを繰り返さなければ、満足な物は作れないでしょう。そういう決まっていない試作などの期間や費用はお約束できるものではないということが理由です。
今回のDT125は全く経験ありませんでしたが、製作できる可能性があったことと、こういう依頼に対応できないと、弊社の存在意義も無いと考えましたので、お引き受けすることにしました。
ワンオフなど安易に引き受けるものではないことを思い知らされる例でした。
DT125といえば水冷エンジンのチャンバーしか経験が無かったのですが、このマシンは空冷エンジンでした。初期型は78年ですがこれは後期型の80年モデルのようです。
依頼内容はRZ125チャンバーのスペックで作りたいということだったのですが、ボア、ストロークが56×50で同じなので使えると思ったのですが駄目でした。ノーマルチャンバーの寸法とRZ用が違い過ぎて、おそらくパワーダウンするだろうと予測したからです。
では空冷エンジンのレーサー用ということで77CR125が56×50で同じボア、ストロークなので使えるのではないかと試作に取りかかったのでした。
これが77CR125スペックですが、試乗してみて落胆しました。
全体的にトルク不足で高速も伸びない、ノーマルより全然走らない失敗作でした。
カタログ値だけの性能比較ですがDTは13PS/7500rpmに対して77CRは22PS/10000rpmということで、同じボア、ストロークでも性能が格段に違うということ。ポート形状やピストン形状など他の要素が大きく違っているためにチャンバー形状も違ってくるということを物語っています。
当時のDTと同じ鋳造型で製造されている80年式YZ125も同じボア、ストロークですが、26.5PS/11000rpmという高回転高出力型の特性を持ちます。一般市販車のDTの性能が違うのは公道での乗りやすさや安全性を重視した結果と考えられますので、やはりノーマルチャンバーをベースに作らなければならないということです。
ノーマルチャンバーは膨張部が2重構造になっていますので、外形寸法からは内部の寸法が測れません。
ストレート部とコンバージェント(収束)コーンは125クラスの過去データーから妥当な寸法を導き出し、推測して決めました。
ようやくワンオフ製作に掛かることができます。
テールパイプがモノクロスサスのショックとクリーナーボックスの狭い隙間をクネクネと曲がって通してあります。こういう部分は実車がないと製作不可能です。
サイレンサーも頼まれましたのでレトロな雰囲気のオールアルミで仕上げました。
試乗してみましたら、ノーマル同様の特性で5000rpmから8000rpmまでパワーバンドが広がる乗りやすいものにできました。
8000rpmからレッドゾーンなので、レーサーのように高回転で回す必要がないエンジンです。
32年前のオートバイなので部品も廃番になっています。壊さないように走り続けていただきたいと思います。
国内のモトクロッサーの排気量では250クラスがスタンダードだと思っていますが、中でも業界のリーダー的存在のホンダが製造しているCRFに力を注いでマフラーを作っています。
2012モデル用ですが
弊社オリジナルの特徴に触れてみたいと思います。
少量生産なのでアルミとチタン板、チタンパイプをハンドワークで加工しています。
フロントキャップの部分です。通常、板物のキャップで作られるパーツですが、アルミ塊から削り出しています。板物の場合、クラッシュして大きな荷重が掛かったときに歪み易いのでアルミ塊の方が荷重に耐えられます。
チタンパイプが圧入してありますが、アルミが熱膨張してパイプが動いてしまうのを防ぐために、キャップ内側にフランジを溶接してボルト止めしてありますので絶対に動きません。
エンドキャップ部分はチタン製です。リヤパイプの内径と長さの適正化により、騒音低減とパワーアップの両立を実現しました。騒音は2mMAX法で楽々クリアします。
菱形断面のアルミパイプは曲率の小さいR曲げと平面の面積を縮小することで、剛性を上げています。ノーマルのアルミサイレンサーより強度が高いと思います。
結合はM5のネジ止めにしてあります。ステレスリベット加締められるエアリベッターがなくてもヘキサゴンレンチだけで脱着できるのでグラスウール交換も容易にできます。
フロントキャップの結合はM6のボルト止めで、こちらもヘキサゴンレンチで脱着可能です。
分解可能にすることで、ダメージを受けたパーツ別に修理したり交換することを前提としていますので、このマフラーのオーナーには、クラッシュしてダメージを受けても使い続けていただきたい思いを込めています。
エキパイとミドルパイプの結合部分はガスケット不要です。
ノーマルのガスケット仕様ですとサブフレームの動きにあわせてサイレンサーも振られますので、ガスケットの内側でエキパイ端末が動いて、潰れてしまっているのを見た事がある人も多いと思います。
0.1mm隙間で嵌め合いしてありますので勘合部分の剛性が上がってパイプ端末が潰れないで済みます。
手曲げエキパイはノーマルと同寸ですが重量は200g軽量、サイレンサーは、なんと1kg軽量になります。
またチタンは錆びないのは勿論ですが、泥汚れもつきにくく、マフラーの素材として理想的です。
製作費はエキパイが2万円、サイレンサーが48000円という量産品並みで提供させていただきますが、ハンドメイドなので納期は業務の状況で変動しますのでメール等でお問い合わせください。
CRM250のチャンバーはARとRR(3型)で若干の仕様変更があります。チャンバー諸元は同じですが、口元フランジの穴位置と下側マウントステーの穴位置が違いますので、ARとRRは互換性ありません。
我社にとって、この10年間で最も売れたチャンバー、サイレンサーがCRM250です。数えてはいませんが200台くらいです。殆どのお客さんは、チャンバーとサイレンサーのセットで注文されますが、勿論どちらか一方でもノーマルに取り付くようになっています。
およそ半数はクローム鍍金を指定されますが、これは外注費として15000円別途かかりますので、総額39000円という少し高価なものになります。私的にはチャンバーは未塗装で焼け色を楽しむものだと思っていますので、邪道と思っていますが、乗りっぱなしでも錆びがでないクローム鍍金の手間要らずで外観がかわらないことは魅力かもしれません。
CRMの実車が近くにありませんので、装着画像は撮れませんが、鍍金工場から引き取って梱包する僅かの時間で完成品画像を取ってみました。
理想は、ラインナップ品は在庫をストックしておいて注文されると直ぐ発送、という形を取るべきですが、何を頼まれるか分らない上に1品あたり15時間程度製作にかかるため、オーダーが溜まってしまいます。通常1ヶ月以上、お待ちいただいているのに在庫品のために時間を割いている余裕がないということです。お待ちいただいているお客様には、申し訳ありません。
チタンパイプに砂を詰めて手曲げします。
これはφ35ですが180°曲げは相当な経験が必要でしょう。
バーナーで炙りながら金属の固さを腕に感じながら柔らかくなったところで曲げていきますが、失敗するとパイプが潰れてしまったり、内Rにシワがよったりします。
曲げ可能な最小Rというものがありますが、これは内Rで45Rです。太いサイズほど曲げRは大きくなっていきます。
ベンダーマシンはありませんので、手曲げ技術だけが頼りの作業です。
YZ250Fのノーマルエキパイを切ったものと比較ですが、遜色ないカーブを描いています。
オフロード用のエキパイはこれができないと形になりませんので必須テクニックでしょう。
フランジの部分ですが、YZは口元が2mm拡大しています。フランジで押さえるためのツバ出し加工もしてあります。
フランジはA2017削り出しです。量産ではチタンやスチールのプレートをプレス打ち抜きやレーザーカットするのが普通ですが、スタッドボルトの締め付けで撓んでしまいますので、A2017の厚さ10mmのほうが、撓まず放熱性も良いので採用しています。
後半のパイプはφ41.3ですが材料代が2mで16000円と高価なもので、2万円のエキパイを1本だけ製作すると完全に赤字です。2本作って材料代が払える程度ですから厳しい商売です。
こんな感じで購入した材料代を回収するために日々、仕事に励んでおります。
何故これを作るかといいますと、ノーマルエキパイに亀裂が入ったり、潰れたりして、修理を頼まれることがあります。修理可能な程度には限りがあります。その場合は新品購入をお勧めするのですが純正品でも相当高価なもので、なるべく出費を抑えたい要望に応えようとしているわけです。
耳の痛い話ですが、80年代のモトクロス全盛期に存在したレース場のうち9割以上が無くなっている現実をご存知でしょうか。
関東では新潟の川西モトクロスコース以外、全てのコースが閉鎖されてしまいました。現在はその後つくられたコースで運営されていますが、コースが閉鎖される理由は幾つかあると思います。その一つに騒音問題というものがあって、コースの近隣住民から苦情を受けて対策を迫られるということがあるようです。
2輪メーカーは、国内においてはMFJ公認車両を製造することが、目的でありますから
MFJ公認レースが開催されて、それに適合した車両が販売されれば目的は達成なのです。近隣から苦情を受けるような場所でレースすることについては対応できないということが現状でしょう。実際、全日本開催コースで苦情がでた話を聞かないですし、市街地であったとしても川口や伊勢崎のオートレース場ではモトクロスの比較にならない爆音でレース開催できていますし、その場所で暮らす人たちの認識の違いもあるでしょう。そんな折、関西方面のコースでも騒音問題で一部車種が走行を断られるという対応をされているようなのです。あちらのコースで走られているお客さんから依頼がありまして、2011モデルYZ250Fのマフラーを消音加工してみました。お客さんの話では2012CRF250レベルだと問題ないそうで、カワサキかヤマハが問題の対照となっているということです。
送られてきたマフラーはYZ250FのUS仕様のサイレンサーとエキパイで、国内のノーマルより当然、うるさいとおもわれます。比較検討のため、ノーマルは手をつけずにUSの方を加工することになりました。
よく暫定的にマフラーの出口にバッフルを装着することがありますが、チューンアップされたエンジン性能を損ねることと、バッフル長が短く、出口付近にあるため風切り音が出てしまい、耳障りな音に変わったりして満足な効果は得られないでしょう。
目的は暫定的な処置ではなく、CRF250並みの消音性能を目指すということで、取り外せる仕様にはなっておりません。
リヤパイプの内径を縮小しつつ、長さも延長しています。排気の吸い込みが有利になるように吸い込み口をテーパー状にしてあります。パンチングの太さはパワーに影響しますので細くしません。
マフラーの容積がCRFより小さいので同等にはならないですが、ノーマルに比べると違いが歴然となるでしょう。
グラスウールが消音する上で重要なアイテムになります。
US仕様に組み込まれていたのは旧型のノーマルグラス&ステンウールでしたので、ホンダ純正に取り換えました。ヤマハさんに申し訳ないですが、こちらの方が消音性能が上なので、純正部品代7600円投資する必要がありました。
CRFサイズは画像の通り量が多いのでYZ用には2割ほどグラスウールを間引かないと入りません。
エキパイもノーマルにサブチャンバーを仕込みました。騒音は1dBほど軽減されますが耳で聞いた程度ではあまりわかりません。
車検で数値ギリギリだったとすると1dB余裕ができるといった具合です。
パワーアップは殆ど変わらないでしょう。むしろ大人しい特性に変わります。直管に横穴が開いてサブチャンバーに入ることになるので排気の勢いが下がり、パワーがマイルドで騒音も少し減るということになります。
マフラーは排気することだけでなく、燃焼室と吸気系が連動していて、排気された分だけ空気が吸入されて適正な燃料がミックスされることで充填効率が上がってパワーアップに繋がるということです。マフラーに蓋をして騒音を下げるという手法は吸入の妨げになってパワーダウンすることになります。
パワーダウンは承知で、そのコースで走り続けるか、問題ない場所まで移動して走るか、いずれにしても最盛期のモトクロスから比較して、やりにくい時代になってきたと思います。
これは、ラインナップではありませんが、お客さんの要望で作ってみました。
アルミの筒とチタンカップの組み合わせですが菱形断面にしました。オーバルより曲率の小さいR曲げにより剛性があがります。
その反面、チタン板の曲げが固くで難義です。プレス機なしで手加工ですから力技で成型しています。
250サイレンサーと同じ形状ですが、450の排気量にあわせて全長で50mm長くしてあります。完成してから2mMAX法で音量計測します。
2012年型CRF450です。オーナーはフラワーオートの嶋野さん。
80年代、ATV協会創世記のころの3輪バギーチャンピオンで、あの"ダミアン号"の運転手でした。60歳過ぎても新型の450でMXでトレーニングする理由は、同年代の仲間が薬飲んでないと健康でいられないのに、MXで体を動かし汗をかくことで体力を維持するためだといいます。
友人が「嶋野くんは本当に薬を飲んでないのか?」と驚いて聞かれたので「MXが薬の代わりだ、バイ〇グラは時々飲むけどな」と笑いとばしたそうです。
サイドカバー付けた状態ですが、サイレンサーエンドの位置がノーマルと同じです。
エンジンかけて吹かしてみましたが、アクセルのレスポンスもよく乗りやすそうです。騒音も思った以上に静粛で、2mMAX法で計測してみましたら110.6dBでしたので250と同等の消音性能を発揮しています。
今年、MCFAJも登録されたそうなのでレースの方も頑張って続けていただきたいと思います。
およそ45年くらい前に製造された車両でしょうか。これは、CSというロードスポーツタイプですが、これと同形式のエンジンを搭載したCLというスクランブラータイプが私の実家にありました。
CL90はオヤジがスクランブルやるために買ったものではなく、会社に通勤するための実用車だったのです。母親は私が8才のときに亡くなっていましたが、記憶に残っていることがあります。
当時、父親は自動車は所有していなかったので、夫婦で買い物に出掛けるときは、オートバイで2人乗りのスタイルでした。まだヘルメット着用は義務でなかったですが、父親はシールド付きハーフキャップ被って、ジャンバーにスラックス、革靴という真面目な服装で乗っていて、母親は頭にスカーフを巻いて、ロングコートの下はスカートでタンデムシートに跨り、ヒールの踵をステップに引っ掛けて乗っかっていました。要するにお洒落着のままオートバイに乗って出かけていたのですね。そんな母親を見て「お母さんは風呂敷被っとった」と父親は言っていました。 40年以上前の話です。
その後、通勤車は自動車に代わったのでCL90は置きっ放しになっていました。私が中学2年になったころ単車に乗りたくて、乗りたくて我慢できずに、親が寝静まったころ、こっそりCL90を持ち出して乗り回すようになりました。クラッチもギヤチェンジも知りません。乗り方教える先生もいません。中学生がたった一人で真夜中の山道で、ライトを頼りに練習していました。真冬で寒かったので、ジャンバーの下に新聞紙を入れて真っ暗な道路を疾走しては、親に気づかれないように返しておく日々が続きました。悪いことは続かないもので、運転に慣れたころに国道を走って遠出したところで警察に捕まって、バレてしまいました。13才のころですから少年法で刑罰はありませんでしたが、夜の監視が厳しくなってしまいました。モトクロス場では13才どころか10才以下でも堂々と単車に乗れるのに、私らが子供のころの環境では非行の元としか見られていませんでした。早く就職して自由に単車に乗ってやると、強く思ったものでした。
このオートバイを見てそんな昔のことを懐かしく思うのですが、今こうやって現役で走っていることが羨ましく感じます。あの思い出のCL90は、私の非行が元で、処分されてしまいましたから。
頼まれたのはメガホンのマフラーですが、レーシング仕様なので消音器は入っていません。浅間火山レースを彷彿される直管です。長さとテーパーの角度はノーマルのマフラーの中身を参考に最適寸法を推測して製作しました。成績を全く気にしない楽しみのためのレース仕様です。
震災があって3月の走行会が中止になってしまって、預かっていたK125が3ヶ月経って、ようやくチャンバー製作着手することになりました。
チャンバーに取り掛かる前に、サーキット走行のためセンタースタンドを外す必要がありますが
フレームを貫通しているシャフトが中で曲がっているのか、全く抜けてこないためスタンド外し不可能でした。
やむを得ず、酸素で溶断しました。
シャフトの生材使用はやめましょう。クロームモリブデン鋼にしましょう。
代わりにレーシングスタンドを作ってから作業開始です。
上がノーマルのマフラー。
2ストシングルなのですが、2個の排気ポートにそれぞれ独立したエキパイということで2本マフラーです。
下が製作したチャンバーとサイレンサー。
エキパイとチャンバーは溶接でワンピースです。
ノーマルは、ダイバージェント(拡散)もコンバージェント(収束)もありません。筒の中に仕切り板があって、反射を起こす構造で、仕切り板の位置を測ってチャンバーの諸元を推定しました。この置き換えは、あまり経験がありませんので、出来上がりの性能が楽しみです。
オーナーが取り付けてあったステップブラケットもチャンバーのレイアウトの邪魔になるので移設させていただいて、スッキリとストレートチャンバーに決めました。
キックアームは始動時にブレーキペダルにぶつかるので、可倒式に交換するべきと思います。
12Vバッテリーつないで、キック始動してみました。暖まっていなくてもアイドリングは安定していて、分離給油のためかワイドオープンにすると白煙がものすごい。回転はストレスなく吹け上がってくるので、走行は問題なさそうです。後はサーキットでキャブセッティングということですが、ここから先はオーナーのお楽しみということで、お引き渡しです。
05年の全日本MX会場の和寒でヤマハのパドック前に展示されたアルミ合金製ハイブリッドフレーム。ハイブリッドとはダイキャストや鍛造という異質な製法で作られたパーツの複合体であるという意味。
そして06年モデルとして発売されたアルミフレームのYZ125が最終仕様という認識でした。
これはお客さんがエンデューロ用に購入したマシンです。
実はYZ125チャンバーは高張力鋼管フレームの時代にラインナップしていましたので、エンジンの基本は大差ないだろうという考えで当時もののスペックで製作しました。
最終型のパイプ形状が若干変更になっており、治具に取り付かないので車体合わせのワンオフ製作です。
我社のチャンバーとヤマハエンジンとの相性は良かったと思います。YZ125に乗った忘れられないライダーがいます。
彼を初めて見たのは守谷のコースでした。
KXに乗っていたA級の若手で、千葉の八街市在住ということで名門習志野レーシングかと思っていました。すると翌年YZに乗り換えて、チーム登録は土浦レーシングになっていたライダーの名は斉藤慎也です。全日本A級でチャンバーサポートして最も好成績を挙げてくれたライダーと評価しています。
01年にA級125クラスで4位入賞でしたが、常にトップを狙う意気込みでした。翌年250クラスにステップアップして、YZ250のチャンバーも作りましたが、トップカテゴリーで15位以内ポイント獲得していましたので若手最有力ライダーでした。
当時チームYZでは、ノーマルで勝てるマシンを証明するということで、社外のパーツ装着を一切禁じていましたが、斉藤選手は「チャンバーだけはこれを使わせて下さい」ということをYZのスタッフに願い出て認めていただいたという経緯がありました。
なんと律儀なことか、作ってもらった物に対する思いというか、なんとしても結果を残したいという意欲が他のライダーと違っていたように思います。残念ながら菅生でヤマハの合同練習中に不慮の事故に遭い選手活動に支障を来たして辞める結果になってしまいました。
そのころから、菅生の赤土の路面は予期できない滑りで頭から落下して死亡したり重症にいたる事故が続いたので路面の改善に力を入れ始めたということで、斉藤選手をはじめ、幾人かのライダーが身をもって危険箇所を教えてくれて、路面の改善を実現してくれたものと感じています。
NSR50のロードレーサーが今回の議題。
GPmonoでレースをされているナオキさんの練習車ですが、ミニバイクは転倒も多いそうでダウンチャンバーだと、サイレンサーは路面に擦ってしまうため
サイレンサーをリヤカウルの中を通す、センター出しに改造するためチャンバーをアップタイプに変更してフレームの中を通すレイアウトに作り変えるというもの。
チャンバーを作るとき、最初にやることは元になるチャンバーの寸法を測ってストレート図に書き直すことです。
写真の上側は元のチャンバー
下側はストレート図に基づいて作られた模型
円盤はパイプの内径を表し、軸芯の棒はパイプの長さを表します。
この模型を曲げて車体に取り回すレイアウトを検討します。
このようにエンジンやフレームとの隙間を確認しながら形状を決めていきます。
同じものは二度と作りません。この車両だけのためのワンオフ製作です。
このあとアンダーカウルやキャブレターの燃料ホースなどに当たらないようにクネクネと複雑なカーブを描いて、狭いフレームの隙間にチャンバーが収まっていきます。
明日は模型の形状に合わせてパイプを成型していきます。
成型されたパイプを接合しました。
模型のカーブに似ていますが、車体がアップチャンバーを想定して設計されていないために取り回しはミリ単位でフレームをかわすシビアなものになりました。
アンダーカウル装着のため、フレームギリギリに寄せないと、グラスファイバーのカウルを溶かしてしまうことになります。
明日はラジエターのマウントとセンター出しサイレンサーのフィッティングを行います。
絶販車のKDX125ですが、時々チャンバー、サイレンサーの製作依頼があります。
車体がなくてはレイアウトが不明のためお断りしてきましたが、今回サイレンサーのみ治具製作してラインナップとしました。
チャンバーはカーブが複雑なので、相変わらず車体持込に限り対応させていただきます。
チャンバーはノーマルのスペックではなくKX125の諸元を用いて、形状をローボーイタイプにモディファイしてあります。
サイレンサー本体はアルミ製、ステンレスパンチングを差し込んで組み立てます。
重量はノーマルが2.2kgに対して0.8kgという軽量さです。
エンドキャップはリベット止めなのでグラスウール交換できます。
価格は¥12000、受注生産で納期は要確認です。
取り付け状態はこんな感じで、
現在バックオーダーで2ヶ月以上かかりますが、お時間に余裕のある方はメール等でお問い合わせください。
時々、質問を受けますので、2ストシングルエンジンのチャンバーをワンオフ製作する場合の費用について通常の解答内容を明記しておきます。
車体持込が前提になりますので、北海道や九州のお客さんから問い合わせられましても対応できかねますので、ご了承ください。
製作の前にチャンバーのスペックを提示いただくか、こちらで過去データーから適当なものをチョイスすることになります。試作テストは別途になりますので既存のスペックによる製作のみ対応します。
新規に製作の場合、型(展開図)を作らなければなりません。型代が¥10000、1本製作でも複数でも変わりません。仮に10本製作なら型代1本当たり¥1000ということになります。
チャンバー本体と型(展開図)
チャンバースペック(寸法)はストレート図で表されているもので、それを車体に合わせて取り回して形状を決定します。
決定したパイプを開いて、展開図となるわけです。
これを罫書きの型として使用することによって同寸のパイプが製作できます。
チャンバー本体の製作費は型が出来ていればシングル1本で¥25000です。
排気量が違っていても工数はあまりかわりませんが、複雑なカーブが多いと¥10000程度割り増しにしていただくこともあります。
ラインナップ品は複数販売できますので、若干割安の機種もあります。
取り付けるサイレンサーが無い場合はサイレンサーの製作も必要です。
最もシンプルなタイプで¥10000です。
チャンバーとの結合はフランジをボルト締めで排気をシールするタイプです。
エンドキャップはリベット止めなので分解してグラスウールを取り換え可能です。
完成すると型代¥10000と品代¥35000でワンオフ製作できます。
材質はSPCC(鉄板)とサイレンサーはアルミを使用した金額です。ステンレスで同スペックで製作の場合は2倍程度かかります。
車体の預かり期間は1週間程度です。
20年経過した車種なので、新規にサイレンサーのラインナップに追加することを渋っておりました。
モトショップ鷹様の熱烈なオファーによりラインナップすることになりました。
上がノーマル、下が今回ラインナップに加えたアルミサイレンサー。
重量はノーマルの2kgに対して、僅か630gという軽量で、重心から遠い車体後部の軽量化に貢献するでしょう。
ノーマルは非分解で生ガスが溜まったら抜けるようにブリザーパイプがついていますが
アルミサイレンサーはリベットをはずして、湿ったグラスウールを交換できるようになっています。価格は特価¥12000也
ですが、現在バックオーダーで2ヶ月分業務が溜まっておりますので3月以降でないと作れませんのでご了承ください。
ラインナップするためには、ノーマルのサイレンサーが取り付くように治具製作しなければなりません。
この治具で位置決めしながら製作しますが
最初は車体に合わせて確認しておかないと
取り付け保証はできませんので、マフラー現品送付でワンオフ製作を希望される場合もありますが、治具製作も含めて了承していただく必要があります。
鷹さんの車両ですが、取り付け確認できると安心できます。
チャンバーとセットでこの様な感じで出来ました。
2スト、旧車のマフラーも続々出てくるでしょう。
現行車は高性能ですが非常に高価格で不景気な今の経済状況だと一部の富裕層しか購入できません。それほどお金かけなくても、いじって楽しめる旧車が時代のニーズに合っているのでしょう。
依頼されてくる車種は大半がオンロードモデルで今回もその一つ。
フランスヤマハ製で新車で2ストローク車を生産していますが
法律で出力規制が掛かっているとやらで
もう少しパワーアップを希望しているのがお客さんの願いです。
ノーマルのチャンバーからは正確なチャンバー諸元が分りません。
そこで過去の同一排気量のデータから適当なものを選んで
形状を車体に合わせて新作しています。
微妙な変更はテストを重ねないと無理ですが、ノーマルより強力な物にするには
レーサーの諸元を引用することで可能となります。
サイレンサーについても、デチューンの対象ですから排気の抵抗を下げつつ消音効果のある物に作り変えます。
オールアルミでバフ仕上げは2ストモトクロッサーで性能実証済みのアイテムであります。
完成後、チョット公道で試乗してみましたが、美味しい2ストのパワーとサウンドで早くオーナーさんに乗っていただきたいと思いました。
今回の依頼にはオプションがありまして、coocaseというボックスつきリヤキャリアの取り付けです。
ボックスはワンタッチで脱着できてツーリングに買い物に役立ちそうです。
但し、この車両にはボックスを装着できるキャリアが装備されていないので新作する必要があったのです。
グラブレールのねじ穴を利用してボルトオンにしてあります。完璧な立て付けです。(自画自賛)
2010モデルYZ250F用のエキパイをラインナップに加えました。
チタニウム製のエキパイとサイレンサーを50mmショートにしてオリジナルリヤパイプに換装しました
エキパイはノーマルと等長ですがレゾネーター付、実用回転域のコントロール性向上と音量の低減が目的です。
サイレンサーはノーマルで音量に余裕があるのでショート化して排気抵抗を減らす目的です。
チタニウム製のオリジナルリヤパイプは騒音と排圧の調整をしたもので
音量は5000rpmで92dB/AでありますのでMFJのレースでも使用可能です。
気になる価格は、
エキパイ ¥21000(税込み)
リヤパイプ (ノーマルサイレンサー組み換え工賃込み)¥15750(税込み)
大分のホンダウイングイワオ様から特注の製作依頼です。
10モデルCRF250Rのエキパイ製作ですが
ノーマルがステンレスと鉄のフランジに対してチタニウムとアルミフランジでリプレイスします。
チタンパイプφ35とφ38.1の2種類を使います・
片方に蓋を溶接して砂を詰めます。
この砂詰めが不十分だとパイプが潰れたり、皺が入って不良品になってしまいます。
1台分のパイプ代が1万円くらいしますの無駄にすることはできません。
量産のエキパイは100%機械曲げです。
パイプを潰さないように曲げるためにはR曲げ専用の機械が必要で非常に高額な投資になります。
我社は高額な投資はしません。なぜなら、お客さんの必要数は1本だけだからです。
1本だけ曲げるのでしたら、このように万力と炙りバーナーだけで充分です。
180°曲げですが熟練した手曲げ技術がないと高価な材料を何本も無駄にしてしまうでしょう。
これができないとマフラー屋とは呼べませんね。
取り回しは車両がありませんので、このような治具を作って合わせます。
イワオさんからノーマルのエキパイと取り付け状態の画像を送っていただき、それを元に車体との位置関係がうまくいくようにゲージを作っておきました。
曲げたパイプをつなぎ合わせてノーマル形状のエキパイが出来ました。
フランジはアルミ板をフライス加工で作ったものです。
ホンダのモトクロッサーはHRCのキットパーツが別売りされていますので純正部品はコストダウンの対象なのでしょう。
やっぱり他メーカー並みにチタニウムにしていただかないと私の仕事が増えてしまいます。
85ccモトクロッサー国産4メーカーとKTMに対応したチャンバーとサイレンサーを製作し、供給して参りましたが、現在のラインナップは以下のとおりです。
ホンダCR85 チャンバー サイレンサー 04以前、05~モデル
ヤマハYZ85 チャンバー サイレンサー 02~モデル
カワサキKX85 チャンバー サイレンサー 05~モデル
KTM85SX チャンバー サイレンサー 06~モデル
主なレース戦歴
CR85 04,05キッズスーパークロスチャンピオン
CR85、YZ85、KTM85SX 全日本レディースで優勝あり
価格4メーカー共通
チャンバー ¥18000
サイレンサー(MFJ対応) ¥12000税込み 送料別途
全機種受注生産です。納期はお問い合わせください。
ホンダCRM250は88年に1型として発売開始されました。
94年には3型としてフルモデルチェンジを経て97年からARとして最終型となりました。同車種のチャンバー、サイレンサーのラインナップは3型(RR)とARの2タイプになります。
取り付け寸法が若干違いますので年式を指定していただければ製作可能です。1型と2型はワンオフ扱いになりますので、車体お持込みに限り対応させていただきます。
チャンバーのスペックは2000年CR250Rの寸法でCRMの車体に合わせて取り回ししました。
従いましてノーマルよりレーサーよりのエンジン特性となります。
表面処理はチャンバーがスチールの未塗装とクロームめっきのどちらか選択になります。
サイレンサーはオールアルミ、バフ仕上げが標準です。
価格
チャンバー(スチール)¥24000
クロームめっきは+¥15000
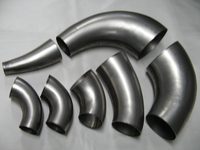
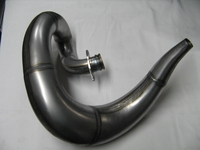