去年からお預かりのビモータ用マフラー、材料が入荷しましたので加工を始めます。
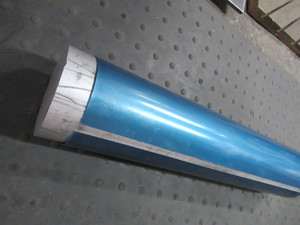
0.8mmチタン2種板のロール曲げです。
長さが、これまで最長の450mmもありますので、いきなり3本ロールでは曲がらないです。
そこで鼻曲げは、このような方法を採りました。
曲げRより小さめの棒を板の端末に当てて曲げます。
この状態でダンプカーのアオリを持ち上げるようにして力任せに曲げます。
この辺はロールでは曲がらないので予め曲げておきます。
ロールベンダーの会社はあるのですが
なるべく内作で加工することがコスト削減の秘訣ですが、知恵と労力は掛かります。
棒に巻き付けて全部巻くことはできません。
曲げRが均一にならないためです。
Rが均一でないと真円パイプ作ることは不可能です。
あとはロールベンダーで巻いていきますが
Rの緩いとこ、キツイとこが出来るのでロールのすき間を調整しながら巻いていく必要があります。
道具があれば誰でも簡単ということはないと思います。
ハンマー持っていても上手に板金できないのと同じです。
材料代も高価なのでお釈迦にしないように慎重に進めていきます。
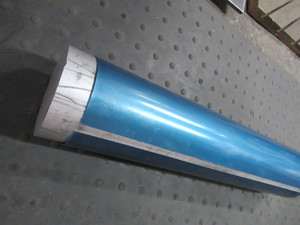
大まかに曲がれば、芯棒に嵌めて形を整えて真円パイプに成形していきます。
450mmのパイプなのでバックシールド用の治具を作りました。
板をお付き合わせして、裏側をアルゴンでシールドして溶接する方法です。
酸化チタンは脆い性質なので、バックシールドして酸化を防ぎます。
付き合わせ溶接できました。
付き合わせの端に溶接棒をチョットだけ置いてナメ付けするだけです。
なるべく止めないで一気にビードを引くようにしています。
熱で歪んでくるので、また芯棒に嵌めて矯正します。
このパイプを基に次の部品が加工されていくことになります。
コメントする